For Tata Hitachi uptime is the key for any heavy earthmoving machinery.
Sandeep Singh, Managing Director, Tata Hitachi. Tata Hitachi manufactures the GI series of excavators in India which are enabled with ‘Consite’. -Sandeep Singh Managing Director, Tata Hitachi Tata Hitachi offers a wide range of mining solution which includes the
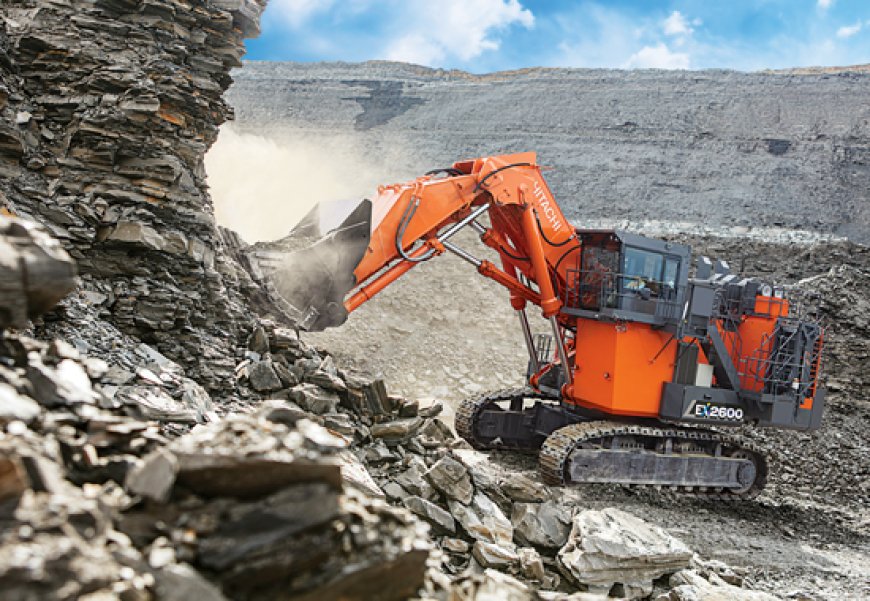
Sandeep Singh,
Managing Director,
Tata Hitachi.
Tata Hitachi manufactures the GI series of excavators in India which are enabled with ‘Consite’.
-Sandeep Singh
Managing Director, Tata Hitachi
Tata Hitachi offers a wide range of mining solution which includes the entire range of large capacity mining excavators from 45T – 120T and above 120T class excavators, wheel loaders, and autonomous haulage systems. “Increase in production has led to upsizing of equipment that is efficient, environment friendly; with advanced health monitoring system etc. as add on features, states Sandeep Singh, Managing Director, Tata Hitachi. Singh shares his views on the mining sector, the opportunities and challenges with EQUIPMENT TIMES.
Commensurate to the projected growth in the mining sector what is your assessment of demand pick up in mining equipment, especially heavy earthmoving equipment?
The mining scenario in India is under a recovery path after a slowdown. Coal is the major driver of this recovery and is now growing in double digits for last several months after Coal India announced aggressive production targets. Various actions taken by Coal Ministry like addition of new rail lines and allocation of additional wagons by railways in coal mining areas have ensured increased despatches.
Metallic minerals like iron ore, after the revised guidelines issued by the Supreme Court, have registered an increase in production.
The recent strategic buyouts by Cement majors like Ultra Tech Cements, Holcim etc in the cement sector is itself an indicator of adding capacity to address the increase in demand. The growth in various sectors is expected to accelerate in the years ahead and this will drive the demand of heavy earthmoving and mining equipment.
Compared to the global scenario, where do we stand in terms of adoption of technology in exploration, benefaction, and in automation etc? What are the challenges here?
Acceptance of proven global technology in mining has been a challenge in past years. At Tata Hitachi, we have taken initiatives like visits to global mining sites, for knowledge sharing amongst the users in the mining industry. This has created awareness and an inclination to implement the latest technology. The technology providers are working toward awareness programmes/training which can enhance implementation. However, technology integration, manpower challenges like skill levels and unions are a challenge for faster adoption of automation etc.
Is there a shift towards the latest and more advanced heavy earth moving equipment of large capacity for opencast mining?
Yes, there has been a shift from conventional equipment to more advanced technology equipment. Increase in production has led to upsizing of equipment that are efficient, environment friendly, with advanced health monitoring system etc. as add on features. The demand for 3-4 Cum (EX1200) and 5-6 Cum (EX1900), buckets size excavators is among the ranges where the growth has happened.
How do you assess the scope of incentivizing investments in the mining equipment sector and encouraging domestic manufacturing of mining equipment & heavy machineries so that cost competitive equipment and spares are available without any risk of foreign exchange fluctuation?
To invest in mining equipment, companies need heavy investments. However, traditionally, the uncertainty in volumes and lack of sustained growth year on year had either limited investment or reduced the interest of the overseas manufacturers to invest in domestic manufacturing.
Having said that there are two segments in the mining sector which we think are important from a manufacturing point of view ie. 45T – 120T and above 120T class excavators. We, at Tata Hitachi, saw this as a long-term opportunity and have indigenised the manufacturing of 45T and 120T excavators more than a decade back itself. We have not only had domestic manufacturing but have also upgraded the technology with the introduction of the ZX470 GI series a few years back. In the above 120T class excavators, the demand is need based and only a few large mines can upgrade to these machines. Hence this category of excavators will continue to be imported in the future.
Manufacturing of complicated spares or hydraulic aggregates needs highly skilled labour and technology and is not cost effective with limited volumes. Less complicated spares can be localised as manufacturers are also responsible to avoid downtime of the equipment. There will always be dependency on imports which the manufacturer must take a risk to absorb foreign exchange fluctuations.
In India, in recent years, stressed assets are highest in public sector banks (PSBs), mainly emerging in selected sectors like mining, iron and steel. Presently, mining lease by itself is non-bankable in India. What is your take on this?
Traditionally, the mining leases have been of long term duration. Due to the cyclicality of the environment the leases were transferred to different operators and then with the intervention of the Supreme Court some of these leases were rescinded leading to stressed assets in the mining sector. The implementation of the MMDR Act and auctioning of mines to specific end use sector has brought in long term players and predictability of operations; hence the outlook for financing is lot brighter now. There are private funding agencies (NBFCs) who have managed to support the leases.
Site optimization, especially through big data seems to be a major trend in the global mining space. How do you assess the potential for the same in the mining sector? Please also elaborate on the technology solution offered by Tata Hitachi and the challenges faced?
With the increase in IoT for heavy earthmoving machinery, this has been well accepted in the global markets and has resulted in improved efficiency in mining as well as site optimization. In India it is still a long way to go as familiarisation of the IoT features with the users/operator is an emerging subject and skill sets to adopt the same is a challenge. However there has been some implementation of productivity enhancing features in the industry. Further load monitoring devices on the equipment give the production of ROM on a nearly real-time basis to monitor onsite production. Therefore, the owner/manager at headquarters can continuously and independently monitor performance apart from getting daily updates from the site.
Tata Hitachi introduced the GI series of machines in the 45T class excavator category with inbuilt features like Consite – IoT platform – for enhancing the efficiency of the equipment and make data available to the customer to improve performance of the equipment. The mining industry is evolving and with cost optimisation driving business, focus on training and adopting newer skill sets will drive more advanced information technology and big data solutions to be used over time.
Could you please elaborate on current aftermarket support trends based on the changing requirement of clients? How geared up is Tata Hitachi in this space?
For TataHitachi uptime is the key for any heavy earthmoving mining machinery and hence it needs a special focus as well as skill set to support the equipment. To address this, we are offering FMC / AMC etc. to our customers, so that we take care of their equipment leaving the customer to concentrate on production from the mines.
We have also been offering MARC (Maintenance and Repair Contracts) as this was the concept which was traditionally working for the users, however due to the uncertainty in production targets, the utilisation of equipment was fluctuating, which made users to think to have a better option would be financially more efficient. Hence the Spares CAP contract has started getting acceptance. Tata Hitachi has been successfully executing the CAP Contracts up to a period of 5-6 years. There has also been investment in training both in-house and overseas, establishment of REMAN centre, etc to handle heavy earthmoving machinery aftermarket support etc.
What is the range of solutions offered by Tata Hitachi in mining & quarrying sector? And also tell us the product and technology trends in that range?
Tata Hitachi manufactures the GI series of excavators in India which are enabled with ‘Consite’ a feature which enable users to see the equipment performance in real-time as well as historically: helping analyse the equipment parameters. We have also introduced the EX2600E electric shovel for the first time in the country in coal mining thereby allowing a higher production at a lower cost and also support in the effort for sustainable mining by reducing CO2 emissions. Apart from the above, the entire range of large capacity mining excavators and wheel loaders are available for the Indian customer, that offer cutting edge technologies from Hitachi with advanced data transmission technologies for continuous real-time monitoring thereby optimizing the utilization of the equipment.
Hitachi Construction Machinery has been in a forefront for development of new technologies in mining equipment like Autonomous Haulage Systems on dump trucks. We have successfully developed dump trucks (EH3500AC-3, EH4000AC-3, EH5000AC-3) which are fitted with proven Hitachi IGBT – AC drives (insulated-gate bipolar transistor (IGBT) is a three-terminal power semiconductor device primarily used as an electronic switch which combines high efficiency and fast switching ). This can also be converted to a trolley option. Some of these dump trucks are already working in coal mining sites in the country. We have a well-established operator training school at Kharagpur to impart training to operators and enhance their skill sets. Apart from this, we have the operator simulator especially for mining applications for enhancing the skill levels of mining equipment operators. This has been well received in the industry
What are the major challenges for the healthy growth of mining equipment, especially heavy earthmoving equipment?
With a large part of buying of large class of mining equipment still driven by PSUs, mining equipment industry in India is guided by the complex buying process involving lot of documentation, as well as acceptance and hesitance in adopting the latest technology. All along in the buying process talks of provenness make the global manufacturers less willing to take risk of promoting their equipment in India as it leads to financial implications. In current framework, technology consideration is still behind while buying mining equipment and that is a challenge for acceptance of any
new technology.
Hits: 147