At TIL Limited, we implement a comprehensive, multi-layered approach to ensure operator safety in high-risk environments
At TIL Limited, operator safety is paramount in our equipment design and manufacturing processes. Our comprehensive safety systems include state-of-the-art features which provide superior protection in challenging operational environments.
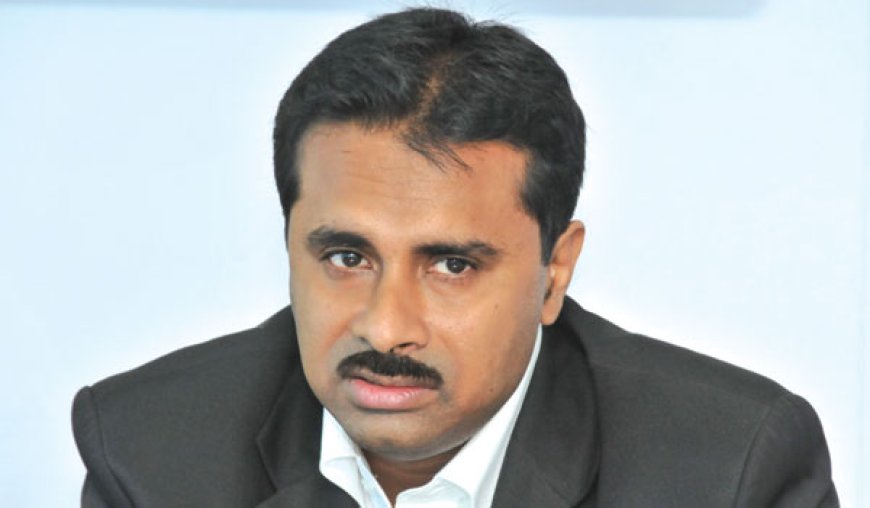
Pinaki Niyogy
Chief Operating Officer & Chief Technology Officer, TIL
What are the key safety features integrated into your equipment? What new advancements have been introduced in your equipment to enhance operator safety?
At TIL Limited, operator safety is paramount in our equipment design and manufacturing processes. Our comprehensive safety systems include state-of-the-art features which provide superior protection in challenging operational environments. We’ve integrated advanced features including the Tilt Lock and Container Clamping System, Automatic Load Sensing Hydraulic System, Hydraulic Safety Lock Valves, and Emergency Stop System, all working in concert to ensure optimal operational safety for ReachStacker.
Our all-glass cab designs provide enhanced visibility, complemented by real-time payload monitoring systems that prevent overloading risks. The ergonomic design of our operator cabins includes adjustable seats and optimized control layouts to minimize operator fatigue during extended operations for ReachStacker. For mobile cranes also, we have interlocks that prevent overloading of our cranes. Since all our equipment comply with various American as well as other International standards, the products are designed with much higher Factor of safety as well as these machines have inbuilt redundancy which prevent any kind of catastrophic failure of our machines.
How do you ensure compliance with national and international safety standards in your equipment?
TIL Limited maintains rigorous quality and safety standards across our manufacturing processes, anchored by our ISO 9001:2015 certification. Our state-of-the-art facilities in Kharagpur and Kamarhati serve as innovation hubs where we maintain stringent quality testing protocols while developing new solutions. This commitment to excellence extends to our strategic partnerships with global leaders like Hyster-Yale, Manitowoc, and Snorkel, ensuring our equipment meets or exceeds international safety standards.
Our testing facilities, including India’s only ReachStacker testing track at Kharagpur, enable comprehensive safety verification under real-world conditions. Every piece of equipment undergoes rigorous testing and quality assurance procedures before deployment, ensuring compliance with both national and international safety regulations. We continuously update our testing protocols to align with evolving global safety standards and incorporate feedback from our extensive pan-India service network.
How do your machines handle features like collision avoidance systems, operator presence detection, or fatigue monitoring?
We have specific in-built features for our ReachStackers like camera based systems which detect proximity and raise alarm and safety systems in which unless the operator occupies the seat, the joystick will not work and the machine will not operate.
How does your company incorporate automation and digital technologies (such as telematics, AI, and IoT) to improve equipment safety? How does your company approach the ergonomics of operator cabins and control systems to enhance safety and reduce fatigue-related accidents?
As part of TIL 2.0, our strategic vision for growth incorporates advanced digital technologies to enhance operational safety. We’re actively integrating IoT capabilities for predictive maintenance and real-time performance monitoring, which significantly improves equipment safety through early detection of potential issues. Our partnership with the Gainwell Group has accelerated our implementation of telematics solutions, enabling real-time monitoring of performance and usage patterns to enhance operational safety.
In terms of ergonomics, our operator cabins are designed with a human-centric approach, featuring all-glass designs for optimal visibility and adjustable seating systems that reduce operator fatigue. The integration of AI-driven analytics enhances decision-making processes and optimizes equipment utilization while maintaining safety parameters. This combination of advanced technology and ergonomic design creates a safer, more efficient operating environment that aligns with our commitment to operational excellence and operator well-being.
How do you ensure the safety of operators working in hazardous conditions (e.g., underground mining or high-risk infrastructure construction zones)? What safety protocols and practices does your equipment manufacturing facility implement to ensure a secure working environment?
At TIL Limited, we implement a comprehensive, multi-layered approach to ensure operator safety in high-risk environments. Our robust safety protocols begin with mandatory Personal Protective Equipment (PPE) requirements, carefully mapped through our detailed PPE matrix for specific working conditions. We conduct thorough Tool Box Talks (TBT) and pep talks at the start of every shift to reinforce safety awareness and address specific operational challenges.
Our commitment to safety extends beyond equipment features to include regular safety committee meetings conducted bi-monthly, ensuring continuous evaluation and improvement of our safety measures.
How do you conduct regular safety audits and risk assessments at your manufacturing plants?
Our safety audit system follows a structured, comprehensive approach that ensures a thorough evaluation of all operational aspects. We conduct regular internal safety audits according to a predetermined schedule, which allows us to systematically assess compliance with safety protocols and identify areas for improvement. These audits are designed to evaluate everything from equipment safety features to workplace practices and emergency preparedness.
The audit process is supported by our bi-monthly safety committee meetings, where findings are reviewed and actionable improvements are developed. This systematic approach to safety assessment helps us maintain high safety standards while continuously evolving our safety protocols to address new challenges and incorporate best practices.
What kind of regular health check-ups and wellness programs are conducted for workers and how frequently?
We maintain a comprehensive annual health monitoring program for all workers, demonstrating our commitment to employee well-being. Our health check-up protocol includes a wide range of diagnostic tests designed to ensure complete health coverage:
The annual health assessment includes comprehensive blood analysis (including TC, DC, ESR, and Hb% measurements), Pulmonary Function Tests (PFT) to monitor respiratory health, and detailed audiometry testing for hearing assessment. We also conduct specific evaluations such as skin scraping tests and specialized eye examinations for operators, ensuring their fitness for equipment operation.
This systematic approach to health monitoring allows us to maintain a proactive stance on employee wellness, identifying and addressing potential health concerns before they become significant issues. The comprehensive nature of our health check-up program reflects our commitment to maintaining a healthy, productive workforce while ensuring operational safety.