ENGINEERING SAFETY THE NEXT FRONTIER IN EQUIPMENT SAFETY
The construction and mining industries are among the most hazardous sectors worldwide, where the safety of workers and equipment remains a critical concern.
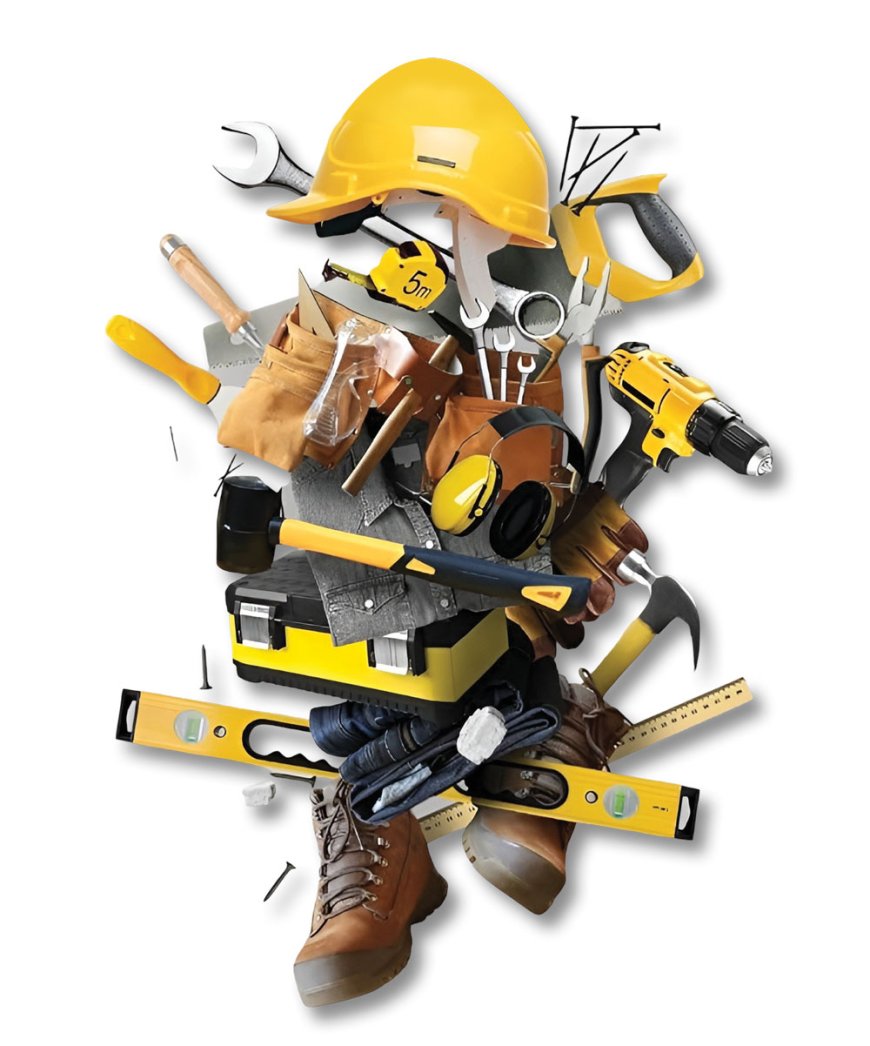
The construction and mining industries are among the most hazardous sectors worldwide, where the safety of workers and equipment remains a critical concern. Despite technological advancements, incidents of accidents and fatalities still occur due to human error, equipment malfunction, or environmental factors. With increasing global regulations, enhanced safety protocols, and innovative equipment features, the landscape of construction and mining safety is evolving significantly. This cover story delves into the current trends, challenges, and advancements in safety measures adopted in construction and mining equipment, with a special focus on India and global best practices.
The Rising Concern for Safety in Construction and Mining
Construction and mining are high-risk industries that involve heavy machinery, extreme working conditions, and the potential for human injury or environmental hazards. According to the International Labour Organization (ILO), thousands of workers lose their lives annually due to workplace accidents in these sectors. In India alone, reports indicate that mining accidents result in numerous fatalities each year, while construction sites contribute significantly to workplace injuries.
As infrastructure development accelerates, the demand for safer construction and mining equipment has grown. Governments and industry leaders are increasingly focusing on ensuring safer working conditions, leading to stringent regulations and a push for technologically advanced machinery that minimizes risks.
Key Safety Challenges in Construction and Mining Equipment
Human Error and Operator Training: A significant number of accidents occur due to improper handling of equipment. Inadequate training, lack of awareness, and human fatigue contribute to mishaps.
Equipment Malfunctions: The failure of critical components such as brakes, hydraulic systems, and electrical circuits can lead to catastrophic accidents. Regular maintenance and real-time monitoring are crucial in preventing such failures.
Harsh Working Conditions: Extreme temperatures, unstable terrains, and confined spaces pose challenges for both workers and machines. Mining activities, especially underground operations, expose workers to life-threatening risks like cave-ins, gas leaks, and dust inhalation.
Regulatory Compliance: In many developing nations, enforcement of safety standards is still a challenge. The disparity in adherence to global safety norms between developed and emerging economies remains a pressing issue.
Safety Regulations: India vs. Global Standards
Governments worldwide have been reinforcing safety laws to mitigate risks in construction and mining.
India’s Regulatory Framework: The Directorate General of Mines Safety (DGMS) and the Bureau of Indian Standards (BIS) have outlined comprehensive safety regulations for mining and construction equipment. The Occupational Safety, Health, and Working Conditions (OSHWC) Code 2020 also emphasizes worker safety through various mandates on PPE usage, accident reporting, and emergency preparedness.
Global Safety Norms: Countries like the U.S., Canada, and Australia have stringent safety regulations enforced by organizations like the Occupational Safety and Health Administration (OSHA) and the Mine Safety and Health Administration (MSHA). European Union standards, such as CE certification for construction and mining equipment, ensure high safety benchmarks. Despite these regulations, implementation remains a challenge, especially in developing economies where enforcement mechanisms are still evolving.
Technological Innovations Enhancing Safety
Advancements in technology are transforming safety in construction and mining equipment. Some of the most notable innovations include:
Automation and AI: Autonomous haul trucks, robotic drilling systems, and AI-powered predictive maintenance reduce human exposure to hazardous environments. Companies like Caterpillar, Komatsu, and Volvo are pioneering autonomous solutions to enhance safety and efficiency.
Telematics and IoT: Real-time tracking of equipment health, fatigue monitoring systems, and geofencing help prevent accidents. Sensors integrated into machines provide predictive analytics that alerts operators before a potential failure.
Advanced Personal Protective Equipment (PPE): Wearable technology, such as smart helmets with augmented reality (AR) displays and real-time hazard detection, is becoming a game-changer in worker safety.
Collision Avoidance Systems: Proximity sensors, radar, and LiDAR-based collision prevention systems are increasingly being integrated into construction and mining vehicles to prevent operator-related accidents.
Dust Suppression Technologies: In mining, silica dust poses a serious health hazard. Advanced ventilation, dust suppression sprays, and air filtration systems are crucial in reducing exposure.
Case Studies: Safety Innovations in Action
India: Tata Steel’s Underground Mining Safety Initiatives: Tata Steel has implemented automation and digital solutions to improve underground mining safety. Their use of remote-controlled drilling, real-time monitoring of air quality, and IoT-based tracking of workers has significantly reduced accident rates.
Global: BHP’s Autonomous Haul Trucks in Australia: BHP, one of the world’s largest mining companies, has deployed a fleet of autonomous haul trucks in its Australian mines. These trucks have not only enhanced safety by removing human operators from hazardous areas but also increased operational efficiency.
USA: Caterpillar’s Smart Construction Solutions: Caterpillar’s Smart Construction Technology integrates machine learning, GPS tracking, and AI-driven automation to ensure safer operations on construction sites. Their fatigue-monitoring systems have been instrumental in reducing accidents caused by drowsy operators.
The Future of Safety in Construction and Mining Equipment
The future of construction and mining safety will be shaped by technological advancements, stricter regulations, and increased industry collaboration. Some key trends include:
Increased Adoption of Automation: The shift toward fully autonomous construction sites and mines will significantly reduce human exposure to dangerous environments.
Stronger Regulations and Compliance Measures: Governments worldwide are expected to tighten safety norms further, ensuring that construction and mining companies prioritize worker safety.
Integration of Green Technologies: Sustainability and safety will go hand in hand, with eco-friendly equipment reducing environmental hazards like dust pollution and toxic emissions.
Enhanced Training and Skill Development: Virtual reality (VR)-based simulators and AI-powered training programs will provide workers with hands-on experience in handling emergency situations and operating heavy machinery safely.
Safety in construction and mining equipment is a multifaceted challenge that requires continuous improvement in technology, regulations, and workforce training. While countries like the U.S. and Australia have set high safety benchmarks, India is rapidly advancing in adopting global best practices. The role of automation, AI, and IoT in preventing accidents is undeniable, and as more companies embrace these technologies, workplace safety standards will continue to improve. As the industry moves forward, collaboration between governments, manufacturers, and construction and mining firms will be crucial in ensuring a safer future for workers worldwide.
Leaders Speak…
V.G. Sakthikumar, Chairman & Managing Director · Schwing Stetter India, said, “At SCHWING Stetter India, safety is a fundamental aspect of our equipment design. Our machines come with advanced safety features such as emergency stop systems, anti-slip platforms, overload protection, and safety interlocks. Additionally, our boom pumps are equipped with stability control mechanisms, and our batching plants feature automated safety locks to prevent hazardous operations. The latest advancements include AI-powered monitoring systems and enhanced hydraulic safety systems, ensuring that operators have maximum control with minimal risk. We strictly adhere to both national and international safety standards, including those set by IS (Indian Standards), and OSHA (Occupational Safety and Health Administration), certification requirements. Our R&D and Quality Assurance teams work closely to conduct rigorous testing and compliance checks before any machine is deployed in the market. We also collaborate with industry experts and regulatory bodies to ensure that our machines meet evolving safety benchmarks. We are integrating smart safety technologies into our machines to ensure maximum operator protection. Our equipment now features collision avoidance systems, which use sensors and cameras to detect obstacles and prevent accidents. We have also introduced operator presence detection systems in some of our machines, ensuring that the equipment operates only when an authorized person is at the controls. Additionally, our telematics-enabled machines monitor operator fatigue, providing real-time alerts to prevent mishaps caused by exhaustion.”
V. Senthilkumar, Managing Director, Propel, said, “Our equipment is equipped with a robust array of safety features designed to prioritize operator protection and enhance overall safety. Key features include an emergency start-stop button further enhances safety. We have also provided guards for all rotating and moving parts, along with hazard and warning stickers to alert operators to potential dangers. Pull cord switch for immediate emergency shutdown, a return roller guard to prevent accidental contact with moving parts and a four-point emergency switch for quick access during critical situations. Additionally, a lockable engine and panel cabinet secure essential components, while a hydraulic folding discharge conveyor minimizes manual handling risks. A platform surrounding the crusher facilitates easy maintenance. Technologically, our machines incorporate a soft start feature that aids in safer loading and unloading, utilizing a proportional control system. Furthermore, the equipment is IoT-enabled, allowing for advanced monitoring and control. Safety decals are strategically placed throughout the machine to reinforce safety awareness.”
Amarnath Ramachandran, Managing Director, Arx Mining, said, “The Arx machines are state-of-the-art and designed with advanced safety features to prevent accidents, enhance visibility, for the safety of the operators and site personnel. We have a whole slew of interlocks in place, to protect the transmission and other critical components from damage. We have dual circuit independent braking systems which are backed up by brake accumulators which are adequately sized to ensure ten full stops after engine or brake/steering pump failure. The dual brake circuit which has independent cross connections to the wheel heads on the bogey axles ensures that in the event of any component like a hose or fitting or even the seals in the wheel head fails, the secondary circuit will kick in and stop the machine. Our machines have GPS monitoring of parameters, faults, and geo location. In addition to these, the machines are fitted with a collision sending radar which will alert the operator that there is an obstruction in the path of the machine. We also have an optional fully autonomous emergency braking system, wherein the machine will stop automatically in the event of the operator failing to react in a timely manner. A Collision avoidance AEBS system is available as an option. This comprises of an array of ultra sound radars which pick up the exact distance and orientation of the obstruction, after this distance is fed in to the vehicle controller a proportional electronic signal is send to the brake actuating valve which will commence braking along with an audible alert. The operator can also simultaneously brake if he so desires as the system takes both inputs. In the event of the operator failing to react in time, the system will stop the machine. Operator presence and fatigue monitoring systems are available off the shelf now.”
According to Shubhabrata Saha, MD & CEO, AJAX Engineering, “At Ajax Engineering Limited, safety is more than a priority—it is a fundamental principle that drives our innovations in concrete equipment manufacturing. We integrate advanced technologies and rigorous design protocols to ensure operator well-being, minimize risks, and enhance overall worksite security. Our Self-Loading Concrete Mixers (SLCMs) incorporate electronically controlled engines that automatically shift to a secure mode if any abnormalities are detected, ensuring smooth and controlled performance. Enhanced visibility solutions, including safety glass, improve clarity in confined spaces such as tunnels and under bridges. Additionally, external drum and water pump control units minimize unnecessary operator movement, reducing fatigue and preventing potential accidents. For Boom Pumps, wireless radio remote control enhances operational safety by allowing the operator to control the machine from a safe distance, particularly in tight and hazardous site conditions. To prevent unintended movements, these safety interlocks ensure that the boom arm is properly rested before permitting the truck to move.”
Narasimha Jayakumar, CEO, Greaves Retail, said, “At Greaves, ensuring the safety of equipment operators is a core responsibility. Regular inspections and preventive maintenance are crucial to identifying and addressing potential issues before they escalate into major operational failures. Each machine comes with a detailed maintenance manual, outlining inspection protocols and best practices. Additionally, our technical experts provide comprehensive check-ups to ensure optimal performance and compliance. All our equipment is designed to meet government-mandated safety and environmental regulations, reinforcing our commitment to safe and sustainable operations.”
Pinaki Niyogy, Chief Operating Officer & Chief Technology Officer, TIL, said, “At TIL Limited, operator safety is paramount in our equipment design and manufacturing processes. Our comprehensive safety systems include state-of-the-art features which provide superior protection in challenging operational environments. We’ve integrated advanced features including the Tilt Lock and Container Clamping System, Automatic Load Sensing Hydraulic System, Hydraulic Safety Lock Valves, and Emergency Stop System, all working in concert to ensure optimal operational safety for ReachStacker. Our all-glass cab designs provide enhanced visibility, complemented by real-time payload monitoring systems that prevent overloading risks. The ergonomic design of our operator cabins includes adjustable seats and optimized control layouts to minimize operator fatigue during extended operations for ReachStacker. For mobile cranes also, we have interlocks that prevent overloading of our cranes. Since all our equipment comply with various American as well as other International standards, the products are designed with much higher Factor of safety as well as these machines have inbuilt redundancy which prevent any kind of catastrophic failure of our machines.”
Amit Bansal, Director, Sales & Marketing, Building Constructions Products (BCP) Division, Caterpillar India, said, “Caterpillar is known for applying technology to machines and job sites in ways that improve customer efficiency and productivity. An equally important goal is using technology to manage and mitigate safety risks for people in and around our machines. Ensuring safety on heavy equipment is paramount to protect operators and bystanders, prevent accidents, and ensure efficient operations, contributing to workplace well-being and productivity. These technologies vary in complexity, beginning with ergonomic improvements inside equipment cabs such as more intuitive controls, easy-to-read displays, and noise and vibration suppression systems that reduce fatigue. An event alerts the operator immediately with an audio alarm and seat vibration inside the cab. The new stylish cab integrates ROPS and FOPS to protect operators and give them a safer environment in which to work. Standard machine comes with spacious cabin, suspension seat, new display, and ergonomic controls for fatigue free operation. We are constantly developing new technologies that help keep workers safe. We take a “big picture” approach when it comes to technology, helping customer’s operations run better, every step of the way.”
Williams R. J., Managing Director, Hailstone Innovations, said, “All products from Hailstone have built in safety features, apart from having higher capacity, excellent quality, efficiency and reliability. Its versatility, safe to operate and easy to handle features are winning the hearts of customers across India and abroad. All our parts last long and our machines have minimum downtime. Our affordable costs with uncompromised product quality have positioned us among the top leaders in the crushing and screening industry. Our products set the standard for quality and are built to withstand the toughest conditions. Our products include crushers, screens, washing solutions, feeders, air classifiers, clarifiers, mobile series and semi mobile series and all come with the latest technology. Hailstone offers a broad range of stationary and mobile solutions with customized designs to meet specific application requirements. These include mobile plants, semi mobile and stationary plants.”
Rajesh Kaul, Vice President and Business Head – Trucks, Tata Motors, said, “As India’s largest commercial vehicle manufacturer, Tata Motors offers a robust Construck portfolio featuring advanced tippers and ready-mix concrete (RMC) solutions tailored for critical applications in infrastructure development. Designed for high productivity, low operating costs, and superior fuel efficiency, the Construck range is well suited for demanding infrastructure, construction and mining environments. Built on a robust chassis with durable aggregates, the vehicles ensure unmatched reliability and longevity. The crash-tested Prima and Signa cabins further enhance comfort and safety. Tata Motors’ VX range of tippers come equipped with Driver Monitoring System (DMS), which proactively monitors driver behavior to enhance safety. Additionally, all our tippers are equipped with features like reverse parking sensors, Hill Start Assist (HSA), engine braking, and automatic traction control. These improve vehicle control, ensure stability on challenging terrains, and enhance safety during operations. Features like HSA prevent rollback on gradients, engine braking reduces wheel brake wear, and reverse parking sensors enhance maneuverability in tight spaces, ensuring safer and more efficient operations. Tata Motors’ tipper trucks with vertical exhaust ensure dust-free operations, and better ground clearance, ideal for mines and construction sites. Complementing these features, Fleet Edge, Tata Motors’ connected vehicle platform, helps strengthen road safety and optimizes operational efficiency. With over 7,60,000 vehicles registered and 80% monthly active users, the platform enables efficient fleet management for businesses while promoting safer driving practices by monitoring driver behavior. Beyond products and value-added services, Tata Motors invests in driver skill development, operating six Institutes of Driving, Training, and Research (IDTRs) nationwide in collaboration with the Government of India. These institutes deliver comprehensive training in modern driving practices, road safety, and professional skills. With cutting-edge products, safety-focused features, value-added services, and driver training initiatives, Tata Motors’ Construck range empowers businesses while prioritizing safety and operational efficiency.”
Sandeep Fotedar, VP, Sales & Services, Aggregates, Metso India, said, “Metso, a global leader in industrial equipment, prioritizes operator safety through a variety of integrated safety features and new advancements. Metso ensures compliance with national and international safety standards in their equipment by adhering to strict industry regulations and implementing robust quality control systems throughout the design, manufacturing, and testing phases. Metso integrates advanced safety features like collision avoidance with radar and LIDAR sensors, providing real-time data, alerts, and automated braking to prevent accidents. Operator presence detection uses seat sensors and interlocks to ensure the operator is in position, with safety systems activating if not. Fatigue monitoring utilizes eye-tracking and wearables to detect drowsiness, alerting operators and suggesting rest breaks. These systems are part of an integrated safety management system, enabling real-time data processing, remote monitoring, and predictive maintenance to enhance safety, reduce accidents, and improve efficiency in hazardous environments. Most of the Metso machines are designed to be stationed at a single location and do not move around during operation. This design ensures stability and efficiency, making them ideal for various industrial applications.”
Amit Randive, Digital Business Line Manager, Digital Solutions Division, Epiroc Mining India, said, “At Epiroc, we’ve long been at the forefront of innovation in the mining and construction industry, with a steadfast commitment to operator safety. Our equipment is designed with the latest safety features, ensuring a secure working environment that prioritizes operator well-being. The days of operator comfort and safety being an afterthought are behind us. With increasingly stringent regulatory requirements and rising customer demand, safety is no longer a nicety – it’s a necessity. We’re proud to be leading the charge in this new era of safety, and we’re committed to continuing to innovate and push the boundaries of what’s possible. Our machines are equipped with the latest safety features inbuilt. The list of features is long but to name a few are- ROPS /FOPS ergonomically designed cab, electronic and smart controls for operators, emergency stops, boom isolation, machine stop controls with human detection in the operation area, pedestrian alert, fatigue monitoring, 360-degree vision system, strata and operation parameters details, speed limiters, safety interlocks, tray warning systems, payload management, live work elimination systems, geofencing, etc.”
Kalpesh Desai, Managing Director, Gefran India, said, “In recent years, the demand for sensors in construction equipment has seen significant growth, driven by the industry’s increasing emphasis on safety, efficiency, and regulatory compliance. The need to enhance operational safety and reduce workplace hazards has led to widespread adoption of advanced sensing technologies. Moreover, the integration of automation and digital monitoring systems in modern construction equipment has necessitated the use of high-precision sensors capable of providing real-time data. One of the most significant trends is the increasing implementation of predictive maintenance systems, which rely on sensors to monitor equipment conditions and prevent failures before they occur.”
Anirban Ghosh, Founder, Nexa Global Infra Solutions (Safeticon), said, “Safeticon (Nexa Global Infra Solutions) represents in India multiple OEM partners each of them is having different categories of equipment with Platform Basket SRL, Italy is specialized in design and manufacturing of Spiderlift from 13 – 54-meter height range, Railroad Access Platforms, Vertical Mast Lifts and Mini cranes, while Multitel Pagliero SpA, Italy designs and manufactures Truck Mounted Aerial Work Platforms from10 meter to 77.5-meter height. Many functional safety features are installed on all types of machines as compulsory devices required for CE certifications. Multitel truck mounted Mobile Elevating Work Platforms (MEWPs) can be equipped with a wide range of advanced features designed to enhance operator safety and improve the overall efficiency of operations. These safety-enhancing features include an automatic control system for chassis inclination, which ensures that the MEWP remains stable even when operating on uneven or sloped surfaces.”
Divy Pachori, Product Manager Room & Pillar, Komatsu, said, “We are constantly making Underground coal mining more productive, easier and safer for all. Our effort is to take the operator further away from harm zone. With the new two way remote, operator can now operate the continuous miner further away from a 30m distance, they don’t have to be part of dust and noise surrounding around the machine and can see cutter drum position and feedback on the remote itself. In addition to this, the online connected miners can be monitored from surface, the maintenance crew is not required to be present always inside the mine or near the machine to get the pulse of the machine. Since the inception of the first Continuous Miner technology in India, Komatsu is pioneer in introducing the products with world class technology to enhance safety & boost productivity and yet again even after more than two decades we are again transforming the Indian mining industry.”
Neville Mevawala, Head of Sales & Marketing, Godrej Material Handling, said, “Ensuring reliability and safety is at the core of our material handling solutions at Godrej. From design to deployment, we integrate rigorous safety protocols that exceed industry standards. To bridge the gap in industry safety standards, we introduced India’s first-ever material handling safety application – the i-Report app. This innovative tool provides a 360-degree safety solution, enabling remote and real-time incident reporting, audits, training, and consultations for our customers and business partners. Additionally, our equipment is designed with inbuilt advanced safety features to minimize operational risks. For instance, our Smart Curve Control Technology automatically reduces speed by up to 30% while turning, preventing tip-overs. The Anti-Rollback System activates every time the brake pedal is released on an incline, preventing unintended movement and enhancing control. Beyond technology, we strongly emphasize operator training and education. Through partnerships with institutes like Gram Tarang in Bhubaneswar, we conduct specialized training programs that not only ensure safer operations but also contribute to skill development and employability in the fast-growing logistics sector.”