Our machines leverage advanced technologies for collision avoidance
Our equipment is equipped with a robust array of safety features designed to prioritize operator protection and enhance overall safety.
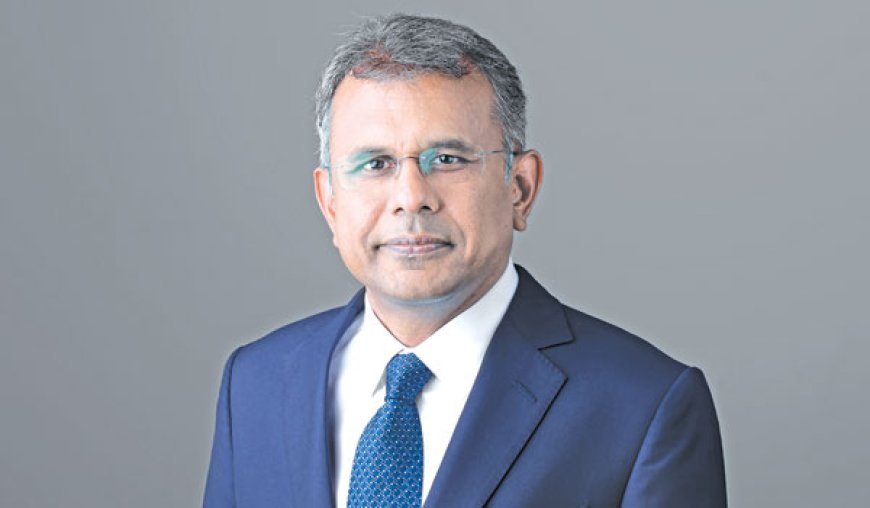
V. Senthilkumar
Managing Director, Propel
What are the key safety features integrated into your equipment? What new advancements have been introduced in your equipment to enhance operator safety?
Our equipment is equipped with a robust array of safety features designed to prioritize operator protection and enhance overall safety. Key features include an emergency start-stop button further enhances safety. We have also provided guards for all rotating and moving parts, along with hazard and warning stickers to alert operators to potential dangers. Pull cord switch for immediate emergency shutdown, a return roller guard to prevent accidental contact with moving parts and a four-point emergency switch for quick access during critical situations. Additionally, a lockable engine and panel cabinet secure essential components, while a hydraulic folding discharge conveyor minimizes manual handling risks. A platform surrounding the crusher facilitates easy maintenance
Technologically, our machines incorporate a soft start feature that aids in safer loading and unloading, utilizing a proportional control system. Furthermore, the equipment is IoT-enabled, allowing for advanced monitoring and control. Safety decals are strategically placed throughout the machine to reinforce safety awareness.
How do you ensure compliance with national and international safety standards in your equipment?
To ensure compliance with national and international safety standards, we adhere to the Mechanical Safety Standard Directive 2006/42/EC on Machinery, as well as the Hydraulic System Safety Standard Directive ISO 13849. Additionally, our machines are CE-certified, demonstrating our commitment to meeting rigorous safety, health, and environmental protection requirements. This certification not only reflects our dedication to quality and safety but also assures our customers that our equipment meets the highest industry standards.
How do your machines handle features like collision avoidance systems, operator presence detection, or fatigue monitoring?
Our machines also leverage advanced technologies for collision avoidance. Collision avoidance systems activate visual lights and alarms when the machine is in motion, providing immediate alerts to potential hazards. A lockout/tag out (LOTO) system ensures safety during operation and maintenance by preventing unauthorized access. Additionally, the programmable logic controller (PLC) system plays a crucial role by displaying errors and providing alarms in the event of any system failures, ensuring that operators are promptly informed of any issues. These integrated safety measures work together to create a secure operating environment, significantly reducing the risk of accidents and enhancing overall operational efficiency.
How does your company incorporate automation and digital technologies (such as telematics, AI, and IoT to improve equipment safety? How does your company approach the ergonomics of operator cabins and control systems to enhance safety and reduce fatigue-related accidents?
Propel integrates automation and digital technologies through ProConnect and ProLive, our advanced IoT solutions designed to enhance equipment safety, optimize performance, and improve operational efficiency.
ProConnect: It is an IoT-driven platform that provides real-time equipment monitoring, predictive maintenance alerts, and remote diagnostics. By continuously tracking machine health, it helps prevent unexpected failures, reducing downtime and enhancing safety.
ProLive: Offering live data insights, it enables operators and fleet managers to monitor critical parameters such as fuel consumption, load conditions, and component wear. This proactive approach minimizes risks associated with manual inspections and ensures the equipment operates within safe limits.
Ergonomics & Operator Safety: Propel prioritizes operator comfort and safety by designing cabins and control systems that reduce fatigue and improve usability:
User-Friendly Control Panels: Intuitive interfaces and ergonomic layouts reduce strain and improve operational efficiency.
Enhanced Visibility: Strategic placement of controls and screens improves situational awareness.
Automated Assistance Features: IOT systems provide real-time alerts for potential hazards, reducing human error.
Vibration & Noise Reduction: Advanced cabin insulation and dampening technologies minimize operator fatigue.
What safety protocols and practices does your equipment manufacturing facility implement to ensure a secure working environment?
To maintain a secure working environment, our equipment manufacturing facility implements a comprehensive set of safety protocols including, Developed Standard operating procedures and Safe Work procedures for all activities, Regular safety orientation training for new employees, and other trainings based on the nature of work, Mandatory personal protective equipment (PPE) use, thorough hazard identification and risk assessments, proper machine safety controls, lockout/tag out procedures for maintenance & Service, clean and organized work areas, Accident / Incident reporting, emergency response plans, and introduced “Zero Harm Safety Incident Policy” to emphasizes our dedication to creating a safe and health work environment, ensuring that everyone returns home without injury & illness every day.
How do you conduct regular safety audits and risk assessments at your manufacturing plants?
We established a structured process to identify potential hazards by inspecting the facility, reviewing documentation, interacting with employees, and evaluating the risks associated with identified hazards, then implementing control measures and monitoring their effectiveness through regular reviews and updates, this includes performing physical inspections, reviewing safety documents, Collecting safety suggestions and concerns from employees, and documenting findings with actionable recommendations to improve safety practices.
What kind of regular health check-ups and wellness programs are conducted for workers and how frequently?
• Pre-employment medical check-up for all new employees
• Lifestyle Education for employees.
• Periodic process awareness trainings to prevent occupational illness.