Wirtgen Group offers a wide range of pavers, concrete as well as for asphalt laying.
P Ramesh, Managing Director & CEO, Wirtgen India. Over the past few years Wirtgen has sold more than 100 slipform pavers for various prestigious road projects across India. Wirtgen Group has been involved with the road development in
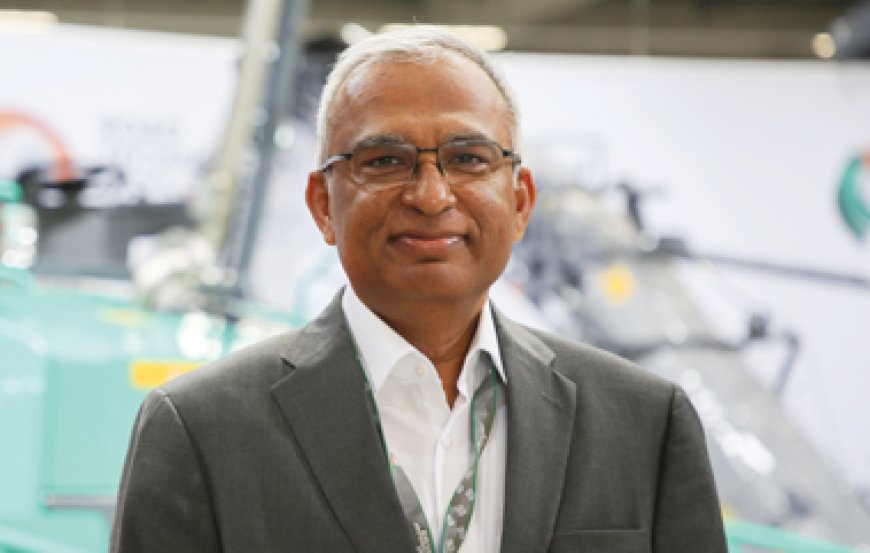
P Ramesh,
Managing Director & CEO,
Wirtgen India.
Over the past few years Wirtgen has sold more than 100 slipform pavers for various prestigious road projects across India.
Wirtgen Group has been involved with the road development in India since the Golden Quadrilateral days starting with the Mumbai Pune Expressway. “Wirtgen provides complete application support for advanced machines as well as conduct an extensive training for the operators from our state of the art training facility at Pune as well as different project sites,” states P Ramesh, Managing Director & CEO, Wirtgen India. Excerpts from the interview…
Tell about the range of pavers offered by Wirtgen in India and what are the latest innovations introduced?
The Wirtgen Group offers a wide range of pavers for both concrete as well as asphalt laying. The Wirtgen slipform pavers for concrete paving are available with a working width of 2.5 meters to 16 meters in a single pass.
Vogele has been the industry pioneer over the last 50 years and have introduced several innovations like the pressure bars and electric heating of the screed, Niveltronic plus operating concept and ergo plus operator features. With our Dash -3 pavers we also offer the eco plus which helps in saving fuel, Auto set plus, Pave dock assistant etc. Vogele also offers several other innovative products like the Spray Jet paver which does the tack coat and paving with the same paver, Mobile feeder which are now being used for building of airport runways and expressways and also the In line paving technology. The most recent innovation from Vogele is the Road Scan which helps the operator of the paver to know the exact temperature of the mic as it is being paved. Sensor pavers play a very important role in getting the right levels and grades when building the roads. The final finish of the road depends to a great extent on the accuracy delivered by these pavers in addition to the mix quality and temperature at which it is laid and compaction.
Vogele has introduced several new technologies like electric heating of screed, high compaction screed with pressure bars, spray jet, mobile feeder, In- line pave, Niveltronic plus for stringless paving etc. With technologies like Inline pave, we are able to pave both the dense bitumen macadam and the wearing course in a single pass operation, as hot on hot , thereby eliminating the tack coat and thus saving in the other costs.
What are the other major benefits of In-line pave on hot on hot paving?
Roads built using twin layer, hot on hot paving techniques can last considerably longer than those constructed using conventional methods. By the elimination of the need for emulsion spraying between binder and wearing courses and with the use of thin layer wearing course designs. Market Leader Joseph Vögele, offer the technology of in line paving of hot bitumen mixes paving the binder layer (DMB ) & Wearing Coat(BC) together in one pass application thus completely allowing the cold joint.
The machines used for the In line paving system are all based on standard units but with modifications, which allow them to carry out the specialized processes. The Super 2100-2IP is the key to the job due to its specially modified, high compaction screed. To achieve the necessary 98% pre-compaction of the binder course the TP2 version of the AB600-2 screed is used. This features altered tamper stroke lengths, a special tamper geometry and special pulsed-flow hydraulics with two pressure bars for high compaction. This is said to provide sufficient compaction of the binder course so that the second paver can operate directly behind on the newly laid mat without risk of sinking into the hot surface and also without the need for the use of rollers in-between the two pavers. Fitted with two 1.25m bolt-on extensions for this job, the screed was used to pave the full road width on this job.
The machines are conventional to operate and an experienced paving crew needs only a relatively short training programme to understand the process. However, a key factor for hot on hot paving is the need for efficient logistics on-site. A reliable supply of trucks transporting both binder and wearing course materials is crucial.
Tell us about the advantages of spray jet over conventional paving with pre-spraying of emulsion?
In many countries, paving binder and surface courses with conventional pre-spraying of emulsion is standard practice when rehabilitating roads. Normally, an emulsion of bitumen and water is applied to the milled base by spray bars and the water allowed to evaporate overnight. This is known as ‘breaking’ of the emulsion. A closed-textured bitumen film remains after the process, which is subsequently overlaid with asphalt. The considerable time and equipment required is a disadvantage of this conventional method. A further problem is that the surrounding areas, roads and curbs are fouled with emulsion by job site vehicles. These problems are now a thing of the past thanks to spray jet technology from VÖGELE. With the spray jet, the fresh emulsion is directly overlaid with asphalt as soon as it is sprayed.
What are advantages of the Mobile Feeder from Vogele?
These high-performance material feeders are the ideal partners on every modern and well organized large-scale job site. The extremely high mix storage capacity and the innovative, heavy-duty transfer concept allow non-stop and non-contacting feed of the paver with mix. The equipment is capable of transferring as much as 1,200t of mix per hour. The trough-shaped and extra wide belt conveyor installed in the feeders provides for an accurate flow of mix and a clean job site.
You spoke about RoadScan which is a recent innovation. Could you elaborate on this?
Making quality measurable is one of the major challenges for contractors and clients worldwide. In road construction, it is particularly important to verify that a constant temperature of the freshly paved asphalt has been maintained, as this is a key criterion for ensuring the quality and durability of roads. As a result, the significance of area-wide temperature monitoring is currently on the rise in an increasing number of markets. With the non-contacting Road Scan temperature measurement system, VÖGELE provide an innovative and economical solution for the road construction sector .The scanning and documentation of the freshly paved asphalt‘s temperature is already specified in tenders in several markets, and in others there are definitive plans to implement this. With its new Road Scan temperature measurement system, VÖGELE deliver the technology required for the job.
And that‘s not all: the system helps road construction teams to continuously monitor the temperature of the supplied mix. What is more, after completion of the construction job, contractors can furnish detailed evidence that the temperature was maintained within the correct range — thanks to the recorded GPS data, including precise tracking.
The high-precision infrared camera is the key component of the VÖGELE RoadScan system. It scans the asphalt pavement behind the screed over the entire area. The housing of the infrared camera also accommodates a high-precision GPS receiver. It records the exact position of the temperature data. The measuring width of 10m comprises 40 grids of 25 x 25 cm-sized tiles. Each of these tiles contains up to 16 single measuring points which are used to calculate a mean value. The measurable temperature range lies between 0°C and 250°C with a tolerance of only ±2°C
What is the scope of two lift concrete pavement and what are advantages of the same?
Two-lift concrete paving involves the placement of two wet-on-wet layers instead of the homogenous single layer commonly placed in concrete paving. Two-lift paving can provide quality surface characteristics, reduce materials costs, and consume recycled aggregates (concrete and milled hot-mix asphalt). This scarcity of aggregates, combined with advances in materials knowledge and construction equipment and increasing demands for pavement surfaces that meet specific noise, durability, and safety objectives are prompting many agencies and contractors around the world to consider two-lift paving as a sustainable solution for building concrete pavements.
What are selection criteria for slipform pavers?
The width of the road and the density of traffic in terms millions of axle loads to be paved is one of the prime criteria in selecting a slipform paver. For an existing state highway which is to be developed from single lane to two lane with shoulders, where the existing road cannot be disturbed due to ongoing traffic, the paving has to be done in 2 passes and you may have to select a paver with width of around 5 m, whereas for a new Greenfield project the paving can be done in a single pass where the no of lanes to be paved would determine the width of the paver required.
Another important criterion for selection is whether the dowel bars are to be inserted manually or automatically, though it is always recommended to use automatic dowel bar inserter to ensure the right quality. The type of the project and the timeline for execution also determines the type of machines to be procured.
Hits: 45