VDMA considers Industrie 4.0 of vital importance in the long term.
Rajesh Nath, Managing Director, VDMA. “Industrie 4.0 allows increase in productivity together with a minimization of personnel costs. Furthermore, German manufacturers and VDMA mining do a lot to keep a leading position in mining technology, especially in underground mining.” Please
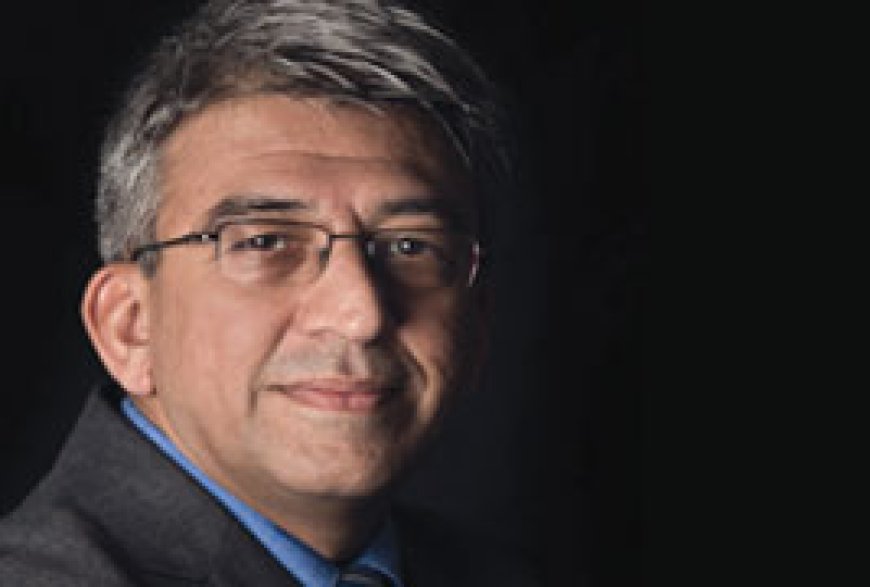
Rajesh Nath,
Managing Director,
VDMA.
“Industrie 4.0 allows increase in productivity together with a minimization of personnel costs. Furthermore, German manufacturers and VDMA mining do a lot to keep a leading position in mining technology, especially in underground mining.”
Please elaborate on the trends in import of mining equipment? What is the outlook for the German mining machinery manufacturers in India?
Mining technology is one of the most export oriented branches of the German engineering industry. For India, Germany is the forth important supplier of mining machinery. In 2016, the total export of mining machinery from Germany to India was to the tune of Euro 25.2 million.
Despite a decrease in exports by 35% last year India remains under the most important markets in Asia. 2016 it ranks number six for German mining equipment manufacturers. With exports worth roughly 26 million Euro it is better than 2014 but worse than 2015 with 38 Mio Euro. In 2015 particularly coal and rock cutters as well as tunnelling machinery has been exported. This didn’t continue last year where numerous crushing and grinding machines were delivered to Indian customers.
Not only regarding the Indian market, German mining machinery manufacturers are glued to a positive outlook on the future. An increasing number of companies are registering a rise in customer enquiries. Some sectors are also developing new areas of business, for example in hard-rock mining. They assume that demand for the raw materials extracted in hard-rock mining will increase substantially as a result of a global expansion in alternative methods of energy production. Manufacturers see the need for raw material producers to reduce costs as a further cause for optimism, since this can only be achieved by increasing efficiency. A global trend toward increasing safety also benefits German manufacturers.
In general, the German mining equipment manufacturers are looking forward optimistic. In Q1 2017 incoming orders and turnover increased by 40% respectively 22%. Until now the economic revival is caused by projects within the European Union and Europe. Input from abroad has not yet arrived.
Could you brief us on the demand-supply trends for surface mining equipment?
The Indian market developed for mining equipment manufacturers relatively favourable last year. For the first eight months exports doubled to an amount of 27.7 million Euro. This is still far away from the peaks reached in 2008 or 2011. But it confirms the hope in an increasing mining business in India. Machines most ordered had been those for crushing or milling of minerals (48%) followed by machines for extraction, roadway driving respective tunnel boring machines (40%).
What is current scenario of underground mining?
India is the world’s third largest producer of coal and has the fifth-largest reserves globally. During 2001-02, open cast mining contributed to 82% and underground mining contributed to 18%. During 2014-15, open cast mining was approximately 91% and underground mining was 9%. Underground mining in India has not been developed due to lack of new underground technologies. SCCL has commenced production from the first of its kind in India, long wall technology in Adriyala Shaft Project in 2014 with a rated capacity of 2.81 MTPA capacity imbibing international standards. It has around 47 mines, of which 16 are open cast mines and 31 are underground mines. In order to achieve the target of 100 mt by 2020, SCCL is planning to start 20-25 new mines in the near future, of which seven mines are expected to start production in FY 2017.
Since 2011, the exports of processing equipment are reduced by 1/3 up to now. It is not probable that the need for processing and beneficiation of minerals is reduced in the same scale. Beside this fact, it is amazing that no extraction technology has been exported to India for years. In this respect it is of importance that there are not so many underground operations in India but the need for mechanization of underground mining is still essential.
What is the relevance of Industrie 4.0 in this context?
VDMA considers Industrie 4.0 of vital importance in the long term, not only to the mining equipment manufacturers but also to German engineering as a whole. Industrie 4.0 allows increase in productivity together with a minimization of personnel costs. Furthermore, German manufacturers and VDMA mining do a lot to keep a leading position in mining technology, especially in underground mining. In order to maintain their leading position, particularly in the underground mining sector, German manufacturers have been involved with Industry 4.0. The industry presented the first machinery to mine coal or other material entirely independently and autonomously in early 2010, and in global comparison is at the forefront of modernising its own production facilities.
What are the trends in processing equipment for the mining sector?
Over the years it is conspicuous that machines for cutting and milling of minerals always rank number 1 in exports from Germany to India continuously worth Euro 5 to 10 million every year, number 2 and 3 alternately are sorting, screening, sizing and washing machines for minerals and parts of drill rigs and deep well drilling machines. But since 2011, the exports of processing equipment are reduced by 1/3 up to now.
What are the challenges of the mining sector?
Procedural and permit delays in mining operations, regulatory and administrative procedures, inadequate infrastructure facilities and sustainability have led to very low FDI inflows in the mining sector historically. Moreover, coal, the largest mined mineral in India, was never opened to commercial mining, resulting in zero interest by global mining majors. However, with the promulgation of the MMDR Act, investment in mining and metals sector is expected to improve as it ushers in improved transparency and speed in licensing and permits.
In the future the Coal Ministry is looking to offer more coal blocks with large reserves to MDOs. This is the right step towards production enhancement. Most importantly their presence will not hinder the growth of the private sector as they can continue with captive mining. The hiring of MDOs along with speedy development of the coal evacuation infrastructure is the way forward for the coal industry. In order to meet the coal demand of the country Coal India Limited (CIL) has also decided to implement some of its mine/projects through the Mine Developer and Operator (MDO) route. At present 54% of the total production is achieved through MDO route.
Hits: 22