TIL-Astec range is designed for enhanced performance and efficient use of energy.
Raj Shrivastav, Executive In-Charge, Crushing & Screening TIL Limited. Our crushing and screening plants are superior by design, amply dimensioned and robust in construction. TIL–Astec provides customers in India a range of track mobile plants, wheeled portable plants, stationery
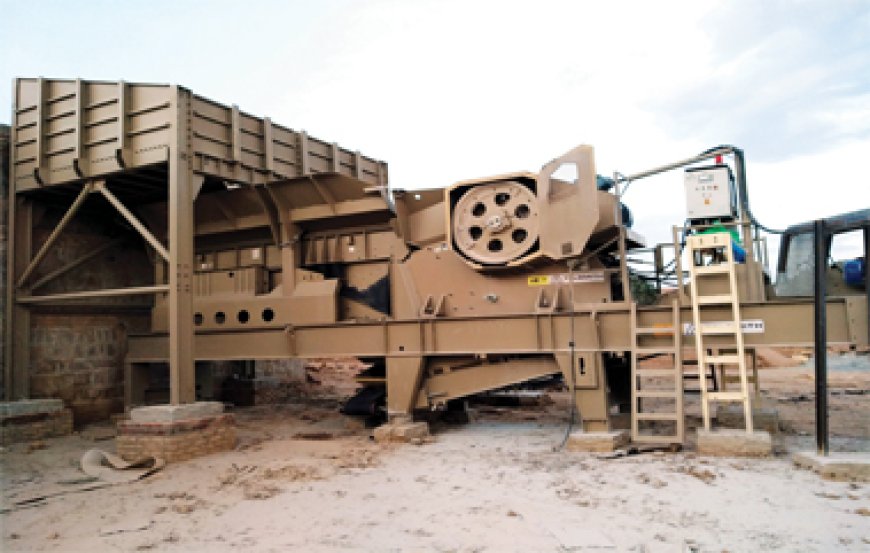
Raj Shrivastav,
Executive In-Charge,
Crushing & Screening TIL Limited.
Our crushing and screening plants are superior by design, amply dimensioned and robust in construction.
TIL–Astec provides customers in India a range of track mobile plants, wheeled portable plants, stationery plants and unit equipment manufactured at TIL’s Kharagpur Works in West Bengal. “The ruggedness and reliability of our crushing equipment, based on the proven technology of Astec Aggregate and Mining Group (AAMG) companies, are among the most important criteria for selecting our equipment,” states Raj Shrivastav, Executive In-Charge – Crushing & Screening. Excerpts from the interview
What is the demand-supply scenario for mid and high range crushers and screens?
To match the pace of the build-up of India’s infrastructure, the demand for mid and high range crushers and screens is certainly set to increase. As per industry estimates, the current CAGR of around 12 – 15%, should continue for the next five years.
What is the growth potential for crushers and screens from the manufactured sand segment?
The excessive harnessing of natural resources has negative externalities, which in turn can make productive economic activities untenable in the long run. Hence, the prohibition on the use of natural sand and the emergence of manufactured sand or M-Sand, whose demand is expected to follow a sustained growth curve. TIL and Astec currently promote the dry process of separating fines in the production of M-Sand, which is effective in terms of productivity, cost of operations and maintenance – giving customers a superior quality in terms of its heterogeneity, gradation and compliance to IS Standards. The dry process, using a High Frequency Screen (HFS), is less expensive with minimum operating cost, easy to maintain and does not use water. However, we are also expanding our offerings to give customers a better choice.
How do you assess the growth potential for static and wheeled / tracked plants from various sectors such as realty, rail corridors and irrigation projects?
Currently, we are witnessing a major resurgence of realty and road projects, both new ones and old projects that were stuck in regulatory and land acquisition issues. With infrastructural development being at the forefront of government initiatives, India will see the emergence of new smart cities and the upgradation / modernization of existing ones. Consequently, we expect a strong demand for crushing and screening plants and equipment, especially portable units, which are preferred for their inter-site mobility. Our products, especially jaw crushers, cone crushers, vertical shaft impactors and other specialized solutions, will also find application in the production of railroad ballast, in light of the aggressive expansion plans of Indian Railways.
What are the product and technology trends in crushers and screens and also elaborate us on the breakthrough technologies in your range?
TIL–Astec provides customers in India a range of track mobile plants, wheeled portable plants, stationery plants and unit equipment manufactured at TIL’s Kharagpur Works in West Bengal (viz. jaw crushers, cone crushers, vertical shaft impactors, vibrating screens and vibrating grizzly feeders) and high frequency screens imported from Astec Mobile Screens (AMS), a part of Astec Aggregate & Mining Group.
The ruggedness and reliability of our crushing equipment, based on the proven technology of Astec Aggregate and Mining Group (AAMG) companies, are among the most important criteria for selecting our equipment. Added to this are the innovative technology incorporated in the design. The Telsmith Hydra-Jaw® range for example features a unique hydraulic toggle, which provides functionalities like fingertip controlled hydraulic adjustment and automatic overload relief eliminating expensive downtime and hydraulic chamber clearing.
Both the Kodiak and SBS range of cone crushers feature fixed shaft type of design. A unique roller bearing design of the KPI-JCI Kodiak® Plus series of cone crushers reduces operating expenses by up to 50 percent, while improving production and energy efficiency. The Kodiak® Plus cone crusher meets coarse and fine crushing application requirements and offers on-the-fly adjustability for easy operation.
The AMS range of high frequency screens operate at around 3600 RPM and above, maximizing screen efficiency and production. A unique tensioning system provides the quickest screen media changes in the market, up to 50% faster than competitive models. Our high frequency screens offer ideal gradation control for reclaiming fines in both wet and dry applications. These high frequency screens of unique design ensure efficient separation in dry processing of M-sand, especially in areas where there is a water shortage.
Brief us on the steps initiated to enhance after sales / back up support?
Crushing and screening equipment are capital intensive assets that are deployed mostly in remote and harsh locations. This class of equipment is thus highly dependent of efficient aftermarket service in order to ensure maximum machine uptime. Availability of spare parts and quick resolution of problems are the factors that differentiate success from failure for equipment manufacturers. TIL has several spare parts stock points across the country and a team of experienced service personnel skilled at trouble shooting and operator training. It is our policy to ensure that the customer’s operating and maintenance teams are duly trained during plant commissioning. Regular visits by our aftermarket support personnel present further opportunities for training on operational and maintenance aspects and troubleshooting of our plants. We believe in supporting our customers all the way from erection and commissioning of machines to the supply of necessary spares and quick problem resolution both during and beyond the warranty period.
Tell us how you have leveraged telematics and big data analytics to differentiate your brand and services?
Telematics is the technology of the future, to ensure not only tracking, set-up and safety of machines, but also better monitoring and data analysis, resulting in predictive maintenance and optimal planning of resources. All these ultimately lead to better performance and life of the assets, and hence, peace of mind for the owners and operators. The Telsmith TRAC10®, for example, is a stand-alone control system that monitors crusher operations, provides automated calibration and setting controls, and protects the crusher from overload; all to yield greater crushing performance and efficiency. Optimum crusher settings are maintained via remote monitoring adjustment using the TRAC10®. Operators can initiate an automated calibration process via the touch screen monitor, that automatically ‘zero’s-out’ and resets to the proper setting.
What are the major parameters a customer looks into while opting for a crushing plant?
Infrastructure projects in India are being fast-tracked, with stringent timelines and quality guidelines. Customers demand shorter delivery times, larger capacities, higher productivities and high availability. There is also a demand for end-to-end solutions combined with strong customer service and support. Faster deployment, greater durability, higher fuel efficiency, lower operating costs, longer service life and superior aftermarket support are the other defining trends in this sector.
TIL-Astec wheeled track crushers find application mainly in the aggregate industry, where the required capacities are small to medium. For larger capacities, stationary plants are the equipment of choice – used mainly in mining and construction projects.
The need for faster deployment of plants has led to a rise in demand for portable and track units, especially with road contractors who prefer inter-site mobility. Most commercial aggregate producers still prefer stationary plants.
Why should a customer opt for your range of crushers / screens?
Equipment from TIL-Astec are designed for enhanced performance and efficient use of energy. Easily replaceable parts make for easier maintenance and lower operating costs. Our crushing and screening plants are superior by design, amply dimensioned and robust in construction, which ensure ease of feeding, processing and extraction of crushed product. Design standardization ensures reduced lead times. Our range of world-class products are further complemented by TIL’s excellent aftermarket support.
What do you think are the major challenges for the healthy growth of the crushers and screens industry? Do you expect any sort of consolidation to take place?
Over the past few years, there has been good acceptance in the market for our products, which has led to a positive upward trend in business. We are confident of accelerating this pace with intense focus in the market, by building capability, increasing market offerings and delivering unmatched service. With the revival of the infrastructure sector and projects being fast tracked, customers will demand end-to-end solutions, combined with strong customer service and support. The foremost challenge will be to ensure higher profitability and productivity for the customer, and ensure availability of trained operators.
Hits: 44