Mobile Automation – Reliable Giants
Builders of mobile equipment can use selected data to optimize their designs, and are able to pursue new business models such as equipment monitoring as a service. Man with a shovel would toil for weeks to move what the high-capacity
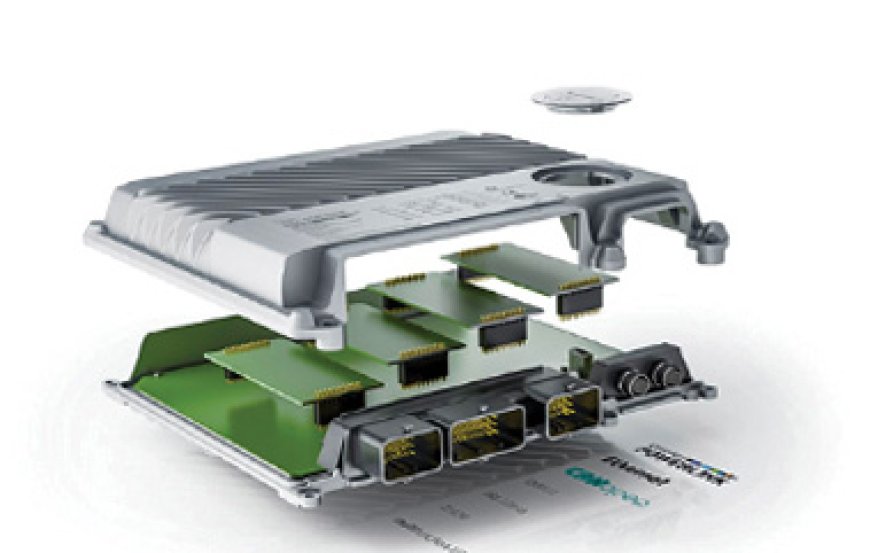
Builders of mobile equipment can use selected data to optimize their designs, and are able to pursue new business models such as equipment monitoring as a service.
Man with a shovel would toil for weeks to move what the high-capacity bucket of a mining excavator can carry away in a single load. Yet, the more earth these massive machines move with each bite, the faster each second of unscheduled maintenance eats away at the bottom line – which is why mining companies go to such great expense to keep their giants healthy. The cost of achieving this crucial reliability can be reduced considerably through intelligent maintenance.
Far from the nearest civilization, towering high above their human masters, gigantic monsters take huge bites out of the rocky landscape. The world’s largest mining excavator is 24 m long, 8.8 m wide, 11 m high and weighs in at 800,000 kilograms. Seated comfortably in the cab a dizzying 10 m off the ground, the driver works the joysticks that control an enormous 47-cubic-meter bucket. In just 20 seconds, the colossal machine moves 80 tonnes of material. “When such a huge excavator goes down, not only does the operator suffer costly losses in productivity, but the ramifications can be felt throughout the entire logistics chain,” explains Stefan Taxer, B&R’s Product Manager for mobile automation.
Preventing unexpected downtime is therefore a top priority. To this end, rotating components like hydraulic pumps, motors and gearboxes are traditionally over-engineered or replaced at conservatively short
intervals.
To keep any downtime that does occur as brief as possible, mining companies keep a sizable stock of replacement parts close at hand. “What all of these solutions have in common is that they incur additional costs,” Taxer points out. These costs can be reduced by applying modern approaches to analytics and maintenance.
Forecasting Faults
As time takes its toll on rotating machine components, even an untrained ear can often hear the difference. “It’s relatively easy to tell when your car has a defective wheel bearing because of the distinct noise it makes,” says Taxer. Mining excavators are so noisy, however, that it is impossible to distinguish any audible change. “This is where vibration-based condition monitoring comes in handy.”
After all, the audible noise is nothing more than vibrations at a certain frequency. A properly configured condition monitoring system will recognize a spike in vibration amplitude in a specific frequency range as the signature of an impending fault. The height of the spike denotes the severity of the damage, indicating how soon a given part should be replaced.
Putting Vibration Data Good Use
“Evaluating vibration data relies on two critical elements,” notes Taxer. On the one hand, you need high-performance hardware that can read the data at a sufficiently high frequency. On the other, you need intelligent software able to detect the tiniest deviations in a huge volume of data.
“Our modular X90 control and I/O system offers the perfect hardware platform,” says Taxer. The heart of the system is the X90 controller with a powerful ARM processor and up to 48 multifunction I/O channels. The modular controller can be equipped with optional I/Os, interfaces or circuit boards – such as the one for condition monitoring.
“Paired with our mapp software components, this results in a very high-performance system that monitors machine health and informs operators in time to take action,” says Taxer. “The mapp components are quick to configure and communicate with each other automatically – reducing the amount of actual programming to a minimum.”
You’ve Got Mail from Your Machine
One example of how mapp components communicate is the interaction between the alarm and notification systems using mapp Alarm and mapp Tweet. “You can easily link these components so that, whenever an alarm occurs, the service technician will receive an email or text message,” says Taxer. This message can inform the technician that a certain bearing is worn and should be replaced within a certain time span.
“As easy as the alarm system is to set up, the most exciting part is the impact it can have on the overall maintenance strategy,” says Taxer, referring to the enormous potential for savings. Condition-based maintenance streamlines spare parts logistics and eliminates the need to replace perfectly healthy components long before the end of their service life.
It even becomes possible to share certain condition monitoring data with the machine builder. “If a manufacturer is able to track the health of their machines, they can drastically reduce the probability of failure,” notes Taxer. This, of course, is also in the best interest of the operator.
Builders of mobile equipment can also use selected data to optimize their designs, and are able to pursue new business models such as equipment monitoring as a service. In this case, the operator is relieved of the fleet maintenance headache and is simply informed when a replacement part will be delivered and installed.
Win-win Situation
This brings Taxer to yet another advantage: “It’s no longer necessary to overengineer so many components.” A fact which, once again, benefits both sides: the manufacturer saves production costs, and the operator pays less for the machine. Since the X90 controller can be connected to existing CAN architectures, it is easy equip an existing fleet with condition monitoring. “It becomes possible to move step-by-step toward a modern real-time bus system that is able to handle the volume of data being generated by today’s machines.” Conventional strategies for preventing unexpected failure of mining excavators are costly and resource-intensive. With B&R’s X90 system and condition monitoring technology, both manufacturers and operators of mobile equipment can generate added value with solutions that make their steel giants more reliable.
Hits: 37