Why an Amman Apollo Plant!
The more we have to construct new roads and maintain the built asset, the more we have to do recycling. This technology, which is very competitive, comes from Europe. Our customers have to reduce the cost and the best way
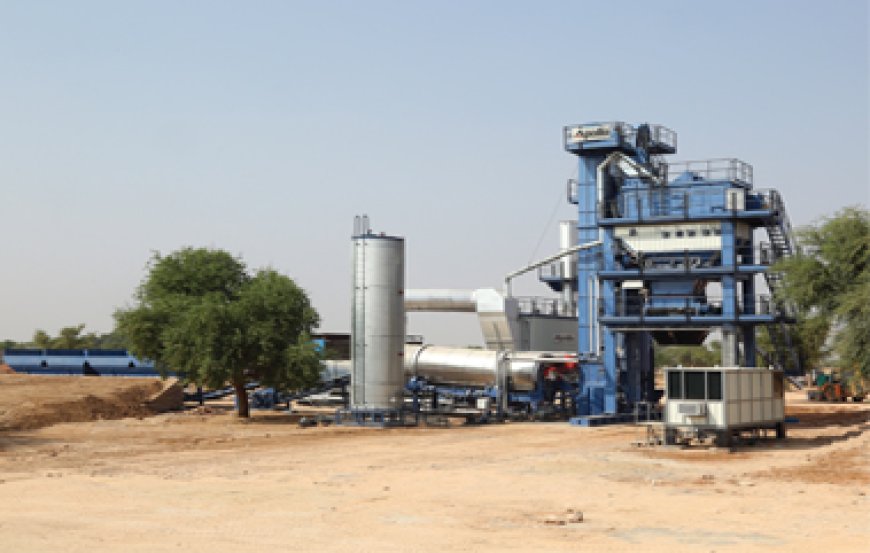
The more we have to construct new roads and maintain the built asset, the more we have to do recycling.
This technology, which is very competitive, comes from Europe. Our customers have to reduce the cost and the best way to reduce the cost is recycling. The simple reason is that the material which is already placed in the road, we can put it back to the plant, and that makes a huge difference in cost as bitumen and aggregates are costly. Recycling has come into the picture now; over the past decade the percentage of using recycled asphalt in road construction has gone from upto 50-75 percent, even 80-90 per cent in Europe. That is a major factor in bringing down the cost, by making use of recycled asphalt in the mix.
That is what makes Ammann mixer a different animal – stronger shovels, pedals, and you can see the full protection that the life span of wear parts provides. For recycling one needs much more intensive mix as one uses recycled asphalt pavement with virgin aggregate and one needs much more shearing force. That is the reason why Ammann mixture powerfully built scores. Another major factor to be considered is energy consumption. To find out what is the energy consumption one needs to have a proper measuring system and the control unit. Our system measures all gas / oil consumption that goes into drying drum, burner, and it also measures kilowatts consumed – and we are giving the feedback. So for each tonne produced, one knows the energy consumption in oil, in electricity etc. We reduce the energy consumption in the dryer which is hundred percent insulated with rockwool, 50 millimetres of insulation. There is different flight arrangement different to the competitors’ one, the raw of lift is taken care that with a strong curtain which ensure proper heat exchange; and the second part of the dryer completely covers the flame, so no aggregates are flying to the flame and it is a clean flame. The burner and the dryer are completely sieved so there is no false air coming into the system.
We have also the same situation in Europe 10 or 15 years ago. The story is very interesting but in our place it is not possible. Then the pressure came from the government that we cannot spoil the natural resources; rather we have to reuse the material already used. The government was forcing the road construction authorities to change. We were forced to learn the art of recycling. And this is a continuous process achieving how to optimally use recycled materials in road construction. So here we are starting with 10 per cent, 20 per cent, then upgrading to 40 to 50 per cent. Recycling process starts when you take the material back, you need to process it as it can be bad in quality. The laboratory need to analyse all the material coming in, proper screening and crushing process needs to be there. The philosophy that rap material is just waste need to be changed. It is highly valuable material with bitumen inside, aggregate inside, so the thinking process has to change; RAP material has to be stored as you store virgin materials.
The road authority has to accept that RAP is of good quality, and then asphalt companies have to learn how to work with RAP. This will take a number of years and I am sure India will be completely different in the next 10-15 years. The more we have to do road maintenance the more we have to do recycling, In Europe the use of RAP is not homogeneous; in Holland they used recycling upto 80 per cent, in Germany, Switzerland and Sweeden; Austria still on the thinking process, but we have already sold two plant with 70-80 per cent. The best situation is competition. In Germany or Switzerland without using a minimum of 50 per cent of RAP you cannot meet the price in the market. This is the best incentive. I have to do it, otherwise, my bid would be too high. This is how it worked in Europe. In Germany and Holland government forced that a bid will not be accepted until it has a certain percent of RAP. The best thing is price level goes down and you cannot survive until you take the RAP route.
The market in china 12-15 years ago when we offered 200 tph plant every one said they don’t require such high capacity plants. They were happy with 120 and 150 tph. But when the government launched the road construction programme the world has ever seen, and the time schedule was stringent and they were forced to replace old plants with high capacity ones as it was more energy efficient, and faster. Today 240 tph is too small for them. The plants what we sell in china, 9 out of 10 is with the capacity of 320 tph.
I see huge road construction programme coming in India, I see the government asking to build road much faster, and Indian contractors will also have to go for bigger plants. In the past the road contracts were small, and what to follow are big projects which justifies the use of bigger plants. It will also change the whole philosophy of road construction. The whole logistics chain from the supply of aggregates, production of asphalt and its transportation to the jobsite, the compaction, everything has to get in line; otherwise big capacity of plants is of no use. But here also I believe the Indian road construction companies will learn so quickly, they will speed up the process, paving technology will change; and that is happening – instead of 6m it will be minimum 10m width which needs higher output from asphalt plants. When the new projects are on there is no other way of doing it.
First of all, the standard introduction of recycling material known as RAP; and the second point is the energy efficiency of the whole plant what we use. The concept what we are introducing of finished product cylo is something different – it helps optimize energy efficiency.
The third thing, we are also offering the technology of low temperature asphalt, which will come up gradually. In Europe it is in production process and there are many proven report from many countries like South Africa and Spain where condition are similar like India. Road authorities need to be convinced; carbon tax which will come globally will force to go into this technology. But in 5-10 years time.
Another major area is the skill level of the operator. The operator is a key man in an asphalt plant and if he is not well trained, the plant also can’t give the required quality output. This is why Amman is offering a simulator, so the plant operator can work on it, and produce 1000 tonnes of asphalt with different mix.
We are also coming out with a training centre at this factory
where we will invite group of our customers not only how to operate the plant but how to operate it efficiently, and how to do the maintenance in a proper way. And that makes a huge difference.
Hits: 114