Volvo IC with Density Direct offer real time density mapping technology.
Dimitrov Krishnan Vice President and Head of Volvo CE India. We have developed a series of initiatives to build awareness of intelligent compaction. Volvo CE has deep roots in India and an established sales and support
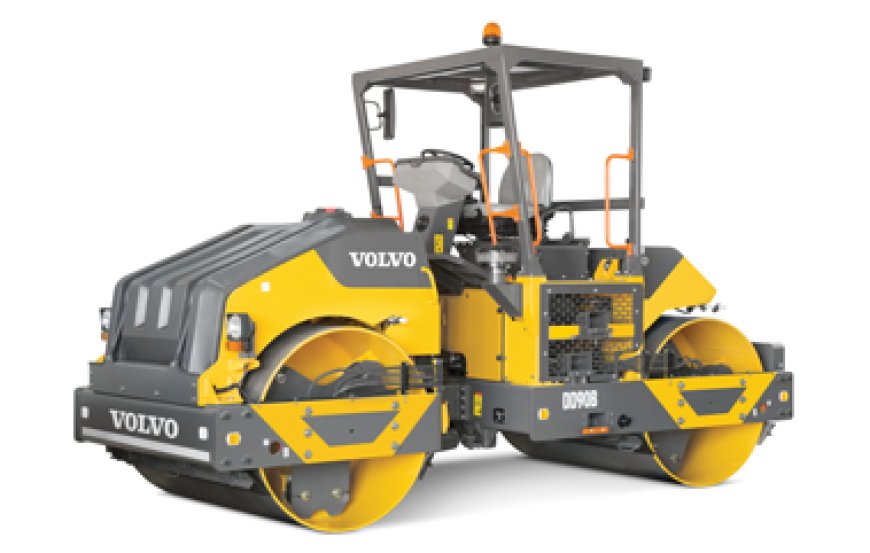
Dimitrov Krishnan
Vice President and
Head of Volvo CE India.
We have developed a series of initiatives to build awareness of intelligent compaction.
Volvo CE has deep roots in India and an established sales and support network. “We are well-positioned to play our own part in the next stage of India’s development and are excited to do so,” says Dimitrov Krishnan, Vice President and Head of Volvo CE India. Krishnan sheds light on the IC solutions offered by the company and the growth prospects.
What role advanced compaction technology such as Volvo IC with Density Direct can play for construction of quality roads?
The Volvo Intelligent Compaction (IC) for select Volvo asphalt compactors is available in two packages — Volvo IC and Volvo IC with Density Direct. In addition to offering the pass mapping, temperature mapping and data storage features of the Volvo IC system, Volvo IC with Density Direct includes the industry’s first real-time density mapping technology.
Density mapping has been described as the ‘holy grail’ of intelligent compaction. For years, contractors have relied on IC systems with stiffness calculations instead of density, which is not the true metric by which contractors are evaluated and paid. With Density Direct, operators have real-time access to the metric that ultimately determines the success of their work, density.
Within the Density Direct system is a calibration screen, where the user sets the target density for the project. Once fully calibrated with data specific to the application, the Volvo Intelligent Compaction with Density Direct system produces a density calculation that is accurate to within 1.5 percent of core sampling, providing a real-time reading of density values over 100 percent of the mat.
With this real-time data, the operator is given the chance to make any necessary adjustments while asphalt is being paved. This not only reduces the occurrence of inadequate densities that drive up project costs, but reduces time spent taking core samples, improves quality, and leads to much greater uniformity than nuclear gauge testing. Calibrations are also “saved” by the compactor, so operators can assign calibrations to certain elements of a job, and quickly switch back and forth between calibrations to meet the demands of specific job elements.
The user interface of Volvo IC with Density Direct depicts a density map, showing each square foot of rolled asphalt in a color representing density, and also provides a real-time numerical density reading displayed in the corner of the screen. Both Volvo IC and Volvo IC with Density Direct offer real-time temperature and pass mapping data. Using the 8”x10” color monitor of the Volvo IC system, the pass mapping function captures each compactor pass and drum overlap with an individual color, so that the operator can easily see gaps and work to maintain uniform coverage. Temperature mapping provides the operator with a temperature ‘map’ that shows the path of the compactor overlaid with the last recorded surface temperature.
What are the factors that prevent the adoption of IC technology by the concerned authorities and end-user segments?
In recent years, we have seen some state governments introduce proposals for Intelligent Compaction measurement systems to support quality monitoring programs. However, the big challenge is still in improving acceptance levels among road contractors, primarily due to the additional cost involved in these systems. We have developed a series of initiatives to build awareness of Intelligent Compaction, partnering with various road authorities through our centre for Road Technology – RASTA (Resource Centre for Asphalt and Soil Training Academy). However, our understanding is that while many authorities are currently assessing options to make implementation a key requirement; in reality it is likely to be some time into the future before we see real change.
Elaborate on the solutions Volvo India provides in soil / asphalt compaction equipment range?
Volvo’s Co-Pilot, for example, offers a range of intelligent machine services – including Dig Assist and Pave Assist – to help operators deliver higher quality outcomes, in less time and with less effort. These examples of automated and assist-functionalities differentiate Volvo’s machines in the market.
In addition, our CareTrack telematics system allows owners to get real-time data on a variety of performance-related features for their fleet. The system generates a wide range of reports, delivering data on aspects such as fuel consumption, operational hours, geographical location and more. The reports are available via a web portal or can be received via SMS or email alerts.
The system can also be used to manage machine servicing and the replacement of parts. This allows fleet managers to reduce fuel costs, optimize machine and operator performance, as well as proactively manage service and maintenance.
Tell us the range offered by Volvo India? What are the features in-built/optional to achieve improved machine performance and productivity?
Our range of asphalt compactors includes the PT220 & DD90B. In the soil compaction category, we offer the SD110BA single-drum compactor.
Available in 22 or 24T configuration, PT220 features a Volvo D5 Tier 3 compliant turbo-charged diesel engine, which is not only more powerful and fuel efficient, but also quieter. This updated machine’s design incorporates safety features, such as an ISO-certified ROPS, sunshade, reversing alarm and automatic engine shutdown.
The PT220 compacts using the forces of mass and manipulation; it can be adapted to a variety of applications by adding or removing ballast or by adjusting tire inflation. The positioning of the tires, four each on front and rear, helps to ensure uniform surface coverage while rolling. The tires’ kneading action against the material surface provides excellent compaction. An isostatic suspension for the front tires helps to keep the roller stable on irregular surfaces as well as maintaining uniform tire contract pressure.
Powered by the premium fuel-efficient Bharat Stage-III (CEV)-compliant engine, the 9T double drum asphalt compactor, DD90B, is engineered to deliver the compaction performance necessary to accommodate the heavy volumes of traffic that the sub-continent’s roads often carry. It is designed to work in conjunction with Volvo CE’s ABG pavers and PT200 pneumatic compactor.
The 11T class SD110BA single-drum compactor is designed to deliver an efficient, powerful performance. Powered by a BS-III compliant engine, the SD110BA combines dynamic drum forces and a heavy drum weight to produce the energy necessary to achieve material target density in fewer passes. The engine and optimized hydraulics work in harmony to provide a smooth, efficient and effective use of energy.
Moreover, our machines offer the Intelligent Compaction system as an option which is fitted directly to the roller. It consists of three central components: the sensor (accelerometer), the processor and the display instrument.
In simple terms, the sensor registers the vibratory movements of the roller drum and information about this is then transferred to the processor for analysis. The information that is analysed is presented on the display as a digital value.
The compaction meter provides a relative measurement of the rigidity of a surface. The measurement increases in line with increases in compaction and is reflected in a rising Compaction Meter Value (CMV). The accelerometer continuously measures the compaction forces that occur as the vibratory drum works on the surface. The signals from this accelerometer change as the surface becomes harder and more stable. These signals are then converted to values that can be relayed to the operator.
How do you look at the future prospects for compactors?
The outlook to 2020 is still very bright. India’s potential is clear, and the drive to improve infrastructure and energy supply will unquestionably facilitate further growth in the economy and the construction equipment industry. As a company, Volvo CE has deep roots in India and an established sales and support network. We are well-positioned to play our own part in the next stage of India’s development and are excited to do so.
Hits: 96