Safety for Mobile Machines
Stefan Taxer, B&R’s Product Manager, Mobile Automation. The Machinery Directive is gaining significance for manufacturers of mobile machinery due to increasing levels of automation, writes Carmen Klingler-Deiseroth. As mobile machinery becomes increasingly automated, its manufacturers must address the requirements of
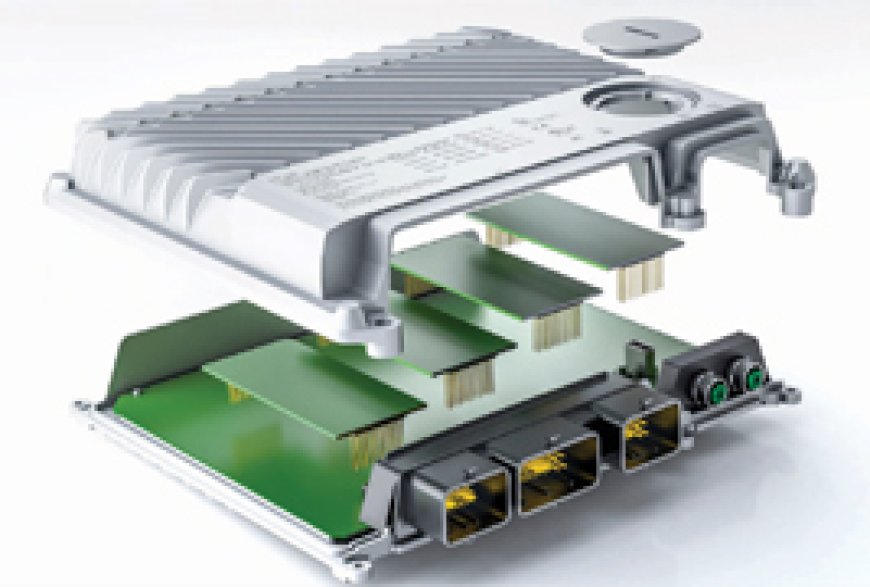
Stefan Taxer,
B&R’s Product Manager,
Mobile Automation.
The Machinery Directive is gaining significance for manufacturers of mobile machinery due to increasing levels of automation, writes Carmen Klingler-Deiseroth.
As mobile machinery becomes increasingly automated, its manufacturers must address the requirements of the European Machinery Directive and the topic of safety technology. To avoid the added cost of developing safety solutions in-house, many of them seek assistance from a reliable technology partner.
The evolving market requirements for mobile machinery can no longer be met with mechanical solutions. Agricultural, construction and municipal vehicles are becoming increasingly automated. That means implementing things like fail-safe drive and steering systems as well as (semi-)autonomous processes. Stefan Taxer, B&R’s Product Manager for Mobile Automation, observes: “The level of automation we see in mobile machinery has skyrocketed over the past few years.”
One of many examples of automated processes are drive-by-wire systems, which transmit information from the gas pedal electrically rather than mechanically. These systems offer many advantages, but are not without risk: “A malfunction while driving could cause a serious accident,” notes Taxer. Safety technology is therefore critical for the drive system.
Identifying the Safety Level
But how does the manufacturer of a mobile machine know which requirements a safety solution must meet? First, they must determine whether the application falls under the jurisdiction of the European Machinery Directive – which is the case for nearly every mobile machine built today. “The Machinery Directive requires manufacturers to carry out a hazard analysis and risk assessment using a risk graph in order to determine the necessary level for the safety function,” explains Taxer. From experience, Taxer knows that mobile machinery must generally achieve safety integrity level SIL 2 and performance level PL c.
According to Taxer, achieving these safety levels is no problem using programmable safety technology. “Nevertheless, many manufacturers shy away from programmable safety technology because they consider it too complex,” says Taxer. He explains that this does not have to be the case – using the B&R system as an example: “For a wide variety of safety functions, there are software blocks available that are pre-certified by TÜV. The task of safety programming itself is thus reduced to simple configuration and linking of the safe software blocks via ladder diagram. The machine manufacturer then only has to prove to TÜV that this work has been carried out in accordance with the guidelines for safe development. This drastically reduces complexity, workload and certification time.
Modular System
The hardware to go with B&R’s programmable safety technology is the X90 safety control and I/O system. The performance of the controller is scalable over a wide range and can be supplemented with functions such as additional I/Os, interfaces or vibration-based condition monitoring. The housing is extremely robust and features IP67K protection.
Future-proof Technology
As a technology partner, B&R goes to great lengths to ensure that its platforms are future proof. If the safety requirements increase to SIL 3 or PL e, for example, there would be no need to redesign the hardware. The controller is already designed to support PL e. “In that case, we’ll simply develop a new option board with the corresponding I/Os that meet PL e requirements,” says Taxer. This board can then be easily integrated into the X90 controller.
B&R also takes great care to ensure that interaction between the standard and safety-related components of a machine application is future proof. The user can imagine the safety solution as a protective yellow shell around the standard machine application. “As long as all the parameters stay within their limits, everything is fine. If a value strays outside its limits, the safety controller takes over and guides the machine into the defined safe state,” explains Taxer. The big advantage of this is that when you modify or expand the machine application, there’s no need to make any changes to the protective shell. Taxer: “That means there is no need for re-validation or re-certification.”
Technology Partner with Industry Experience
The Machinery Directive is gaining significance for manufacturers of mobile machinery due to increasing levels of automation. Automation specialist B&R has ten years of experience in the field of functional safety and in implementing the directives in industrial applications. This experience applies equally well to the agricultural, construction and municipal sectors. “With our comprehensive hardware and software platform and easy-to-configure engineering modules, we are the ideal technology partner for developing safety solutions for mobile machinery,” says Taxer with conviction.
Hits: 102