We are in the process of implementing Industry 4.0 with interconnected processes with real-time data capturing and display
The CE manufacturing in India has come a long way from being largely imported in the early to late nineties to a large part being manufactured locally to cater to the evolving customer requirements and tough local operating conditions.
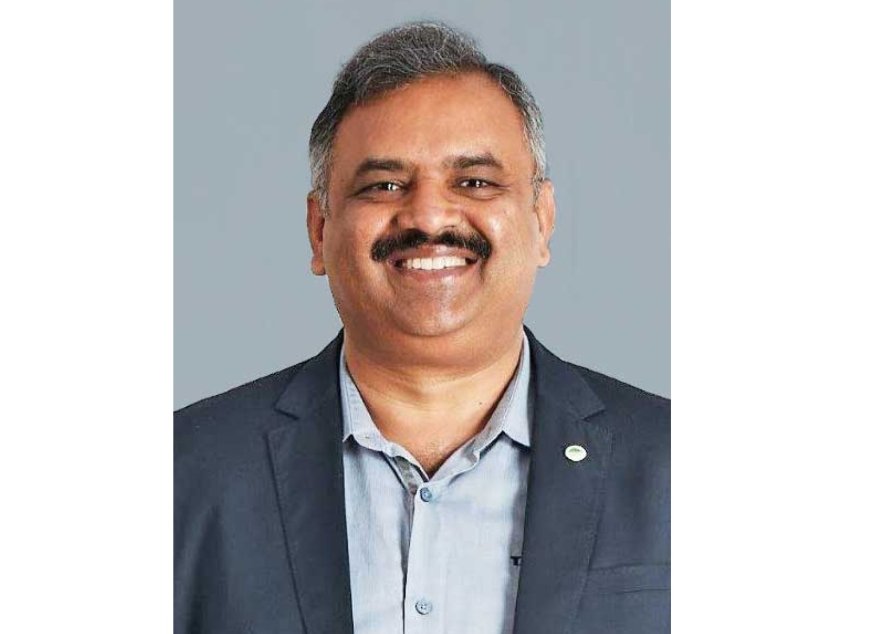
BKR Prasad
Head – Marketing & Product Development, Tata Hitachi Construction Machinery Company
What are your views on India as a global construction equipment manufacturing hub?
The CE manufacturing in India has come a long way from being largely imported in the early to late nineties to a large part being manufactured locally to cater to the evolving customer requirements and tough local operating conditions.
Starting from Backhoe Loaders, Mobile Cranes & Excavators, manufacturing in India now caters to most part of the CE market comprising Compacting Equipment, Drills, Crushers, Concrete Equipment, Batching plants, Pavers, Graders, Mining Dumpers, Crawler Cranes, etc. With volumes going up in line with the sustained growth of Indian Infrastructure investment over the last two decades, increased cost efficiencies have been achieved through modern technologically advanced design & manufacturing processes to an extent that most of the Indian Construction Equipment are very competitive in the international market where they are specifically required.
Several OEMs including Tata Hitachi manufacture & export a wide variety of Construction Equipment to the Global markets ranging from the Middle East, Africa, South East Asia as well as far as Europe, Latin America & North America.
However, several challenges remain from a rapid and unprecedented increase in input costs, supply side disruptions due to freight delays, high freight costs, vessel uncertainty induced by the pandemic as well as recent disruption from the Russia-Ukraine conflict.
The industry association ICEMA is closely working with the government to alleviate some of these issues as well to encourage increased investment in manufacturing to further enhance global competitiveness by increasing localization of critical components to the benefit of the country’s economy from exports as well as to enhance employment opportunities.
Give us details about your manufacturing facilities in India?
Tata Hitachi has manufacturing facilities in Kharagpur and Dharwad. Both the Plants have the latest technology in CNC machining centers, Robotic centers, and a wide range of fixtures and manipulators for manufacturing world-class products. The facilities available are supported by highly skilled manpower to produce components and machines of the highest quality. Also, we emphasize continuous improvements in the processes by developing a culture of innovation amongst all employees through Kaizens & low-cost automation.
Kharagpur: The largest Construction equipment manufacturing facility in South Asia. This is a state-of-the-art plant (Spread over 250 acres) with an integrated facility for component manufacturing and assembly of final machines. This Plant manufactures Hydraulic Excavators starting from 20-Tonne to 120-Tonne class and Wheel Loader from 3-Tonne to the newly launched 5-Tonne.
Kharagpur plant has comprehensive manufacturing processes like Material cutting and preparation, Welding, Heavy and Light machining, Painting facility including Electro dynamic painting of Sheet metal parts, Assembly facility, R&D facilities catering to a wide range of testing setups, Full-fledged Design and development facilities, Tool room facility for Production support, 10.5 MW Solar power plant to cater to Power requirements and lower our Carbon footprint by using renewable energy, Zero discharge plant with facilities like Effluent Treatment plant, Water treatment plant, Sewage treatment plant and a Green Building certified Administrative office.
This plant has so far produced more than 20,000+ machines since its inception in 2009. This plant has been recognized by Hitachi Construction Machinery (HCM), Japan as a hub for exporting machines to its global network. So far, this plant has exported 1400+ machines to different parts of the world.
Dharwad: Spread over 118 acres, the manufacturing facility in Dharwad is operational since 1999. This plant manufactures Hydraulic Excavators up to 20-Tonne class and Shinrai Range of Backhoe Loaders.
The Dharwad plant is continuously upgrading its facilities to improve its capacity & capability focusing on improving the Safety, Quality & Delivery parameters considering the environmental aspects. The current major facilities in the Plant are, Assembly shop for
Mini Excavator, Midi excavator, and Back-hoe loaders, Fabrication & Machining facilities, Transmission assembly shop,
shot blasting shop for fabricated components, Paint shop for fabricated components & sheet metals, Testing and dispatch complex, Incinerator for burning hazardous waste, and Sewage & Effluent Treatment Plant to achieve Zero discharge from Plant.
This Plant has manufactured more than 75,000 machines till-date to cater to both Domestic & Export market demands.
How technologically advanced are your manufacturing facilities in India? Also, what are the safety features incorporated in these facilities?
Both our plants have state-of-the-art manufacturing facilities in all the processes being used such as the high-end Robots used in Welding, CNC machining centers, Cutting-edge painting facilities including ED painting lines, and the Latest Conveyorized assembly lines as well as manual workstations. Also, we are in the process of implementing Industry 4.0 with interconnected processes with real-time data capturing and display.
Safety features like Automatic stoppages of machines for interruption through sensors for the safety of humans, Poka-yoke to minimize the errors to impact the operator’s safety, etc, are incorporated.
What are your company’s initiatives in skilling and training?
Tata Hitachi has a two-pronged approach when it comes to skilling & training:
Permanent employees & Contractual staff-
- On-the-job training in different trades like Welding, Fitting, Machining, Painting, and Mechanical and Electrical maintenance in our production setup
- Skill development through theoretical training and training setups for different skills
- Training is imparted through Skill Training Center inside the plant, which has world-class facilities & Hitachi certified trainers
- Tata-Hitachi JIM Program (Japan India Institute for Manufacturing) in line with Skill India Initiative to train in different skills.
Skill Development Training for youths from local communities: We have an Operator training center with a facility for training on operating Construction Equipment like Hydraulic Excavators, Backhoe Loaders, and Wheel loaders. This setup is elaborate with experienced trainers from across the country imparting training. This is backed up by a State-of-the-art simulator for machine operation conditions simulation which gives near real-life machine operating conditions for the trainees. Once the course is completed the participants are given certificates in collaboration with GOI which help them to get a job as Machine Operators easily across the country.
Hits: 1