Statue of Unity
A landmark that is twice as high as Statue of Liberty in New York and nearly 100 feet higher than the current record holder, Spring Temple Buddha in China. The construction of the Rs 2,989 crore project began in
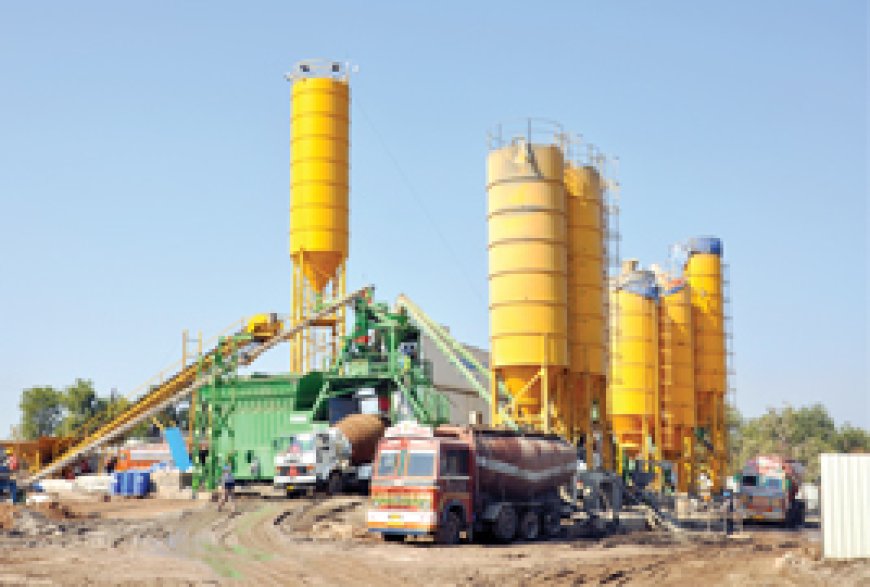
A landmark that is twice as high as Statue of Liberty in New York and nearly 100 feet higher than the current record holder, Spring Temple Buddha in China.
The construction of the Rs 2,989 crore project began in December 2014.The Statue of Unity was built with 210,000 m3 of concrete, 22,500 MT of cement, 6,500 MT of structural steel and 1,850 MT of ‘kansa’ (bronze). The record breaking world’s tallest ‘Statue of Unity’ is 182 m high from the road entry and 208.5 m high from the river entry. Otherwise known as the Unity Statue, the statue honors India’s First Deputy Prime Minister, Sardar Vallabhbhai Jhaverbhai Patel. He earned the title Iron Man of India for his iron will and nerves of steel. He played a key role in unifying India’s 565 princely states into one great Republic of India.
The prolific Indian sculptor
Ram V. Sutar, who is noted for his massive, life-like renderings, was selected to design the statue. MGA&D, the design architect and member of a multi-firm consortium was tasked with delivering the project, is responsible for design and construction oversight of the Statue of Unity. The statue is being built at the Sadhu-Bet Island, approximately 3.5 km south of Sardar Sarovar Dam at Kevadia in the Narmada district of Gujarat, India.
Construction
It took 56 months to complete the project; 15 months for planning, 40 months for construction and two months for handing over by the consortium. Indian infrastructure company Larsen & Toubro won the contract on 27 October 2014 for its lowest bid of 2,989 crore (US$450 million) for the design, construction and maintenance. They commenced the construction on 31 October 2014 with over 3000 workers and 250 engineers worked day and night to complete the project in time.
The RCC spine of the statue
The internal twin concrete cores are the main structural support, around which the entire statue is supported and built upon. The twin cores will serve as the primary structural support, which consumed mammoth 160,000 m3of reinforced cement concrete. Producing, moving and placing 210,000 m3 of concrete was a huge challenge in the entire project, which was eased by using the following Schwing Stetter’s concrete equipment. Larsen & Toubro Limited is one of the largest and most respected companies in India’s private sector were entrusted with the execution of the project. With over 72 years of a strong, customer focused approach and a continuous quest for world-class quality, L&T has unmatched capabilities across technology, engineering and construction, and maintains a leadership position in all its major lines of business.
“Manufacturing, moving and placing one lakh sixty thousand cubic meter of concrete was one of the most challenging part of this project and Schwing Stetter was our obvious choice because of their technology, expertise in application and on whose support we could blindly rely on, stated Prakash R, Head (P&M), L&T, Statue of Unity project. Speaking about the service back up provided by Stetter Prakash had this to say. “To sum it up in few words, ‘they were always there’. They were like a part of L&T, they were working professionally, efficiently and their technical expertise can never be undermined. We typically handed over the entire responsibility of concreting to Schwing Stetter India. We took a back seat and we never faced any issues.”
“Since concreting was happening almost on daily basis, we had difficulty in giving the equipment for periodic maintenance. Since, periodic scheduled maintenance is essential to avoid and prevent any failure; Schwing Stetter’s service team started carrying out their scheduled maintenance during night time for all equipment, thus making the machinery available for concreting during the day time and preventing any possible breakdown. Such was the determination and grit, Schwing Stetter exhibited in supporting our company and helping us to progress with the work in the planned time frame, said Prakash.
He further added, “We wanted zero down time for any of the products, concreting was happening round the clock and any break-down could be a nightmare. So, we have trusted Schwing Stetter’s quality for a long time and we always prefer original OEM parts for reliable operations. Also, here I would like to add that this site’s geographical location is in itself a challenge, being remote and we could completely trust Schwing Stetter for spares supply with less lead time.”
Challenges
High Strength Cold Self-compacting Concrete: The internal twin core being the main vital structure, had to be built with a high strength concrete which was achieved by using temperature controlled concrete. Concrete was manufactured with the assistance of chilling plants, which will bring down the temperate of the aggregates used and thus eventually manufacturing high strength cold concrete (M65-SCC), its temperate was far less relative to the environmental temperature at the time of application.
Concrete Placement: Concrete was placed at a maximum height of 182 m. Multiple pumps were employed to achieve maximum placement of concrete in minimum period of time. Two numbers of Schwing concrete boom pump S36 X were employed to do concreting for the raft (foundation), which consumed a gargantuan quantity of concrete. Once the foundation concrete was done, the next challenge was to build the twin concrete core, with time being a luxury, concrete placement had to be completely mechanized to complete the project within the stipulated time frame.
Major Advantage
Apart from employing one of the most powerful concrete pump ever manufactured Schwing heavy duty concrete pump SP 8800 with 400 KW power, which can displace 116 cubic meter of concrete in an hour, what was essential is the mechanization in placing the pumped concrete. To achieve the same, Schwing separate placing boom (SPB 35) was employed. Concrete was pumped to a massive vertical height of 182 m; the concreting for the internal core was achieved with ease with the use of Schwing separate placing boom vertically.
Unique application:
Schwing separate placing boom application: Significant application hurdle was circumvented by using ACS (Auto Climbing System) for SPB climbing, SPB climbing mast was integrated directly with the outer Peri form work.
A significant portion of the project entailed engineering and reinforcing this rocky outcrop in the middle of the Naramada river bed in order to accommodate the massive sculpture and the base on which it sits which will, when completed house visitor services, and a series of display halls dedicated to Sardar Patel; the history of India’s struggle for and ultimate achievement of independence, and the construction of the statue itself.
The Statue of Unity will become a highly sought and prominent travel destination for both domestic and international audiences. The project will provide an engaging and memorable experience which will include architectural and experiential features such as a memorial and visitor’s centre with cable suspended stretched skin canopy, interactive museum, expansive food and beverage market and a breath taking viewing deck 160 meters above the waters of the Narmada River. It also has a 320 m long designer bridge connecting Sadhu hill to the mainland, 4-lane approach road, administrative complex, 3-star hotel and a conference centre. It can accommodate up to 200 visitors at a time and will provide sweeping, picturesque views of the nearby Sardar Sarovar Dam, Narmada River, as well as the lush Shoolpaneshwar Wildlife Sanctuary that surrounds the site and extends for miles around.
Hits: 373