L&T is in the process of digitalization of parts and service operations.
Komatsu’s ‘Komtrax’ uses satellite-based information communication technology (ICT) to provide constant monitoring of every machine. Arun Pai, General Manager-Product Support, Larsen & Toubro Limited. L&T has state-of the-art service centres at 6 locations fully equipped to carry out complete
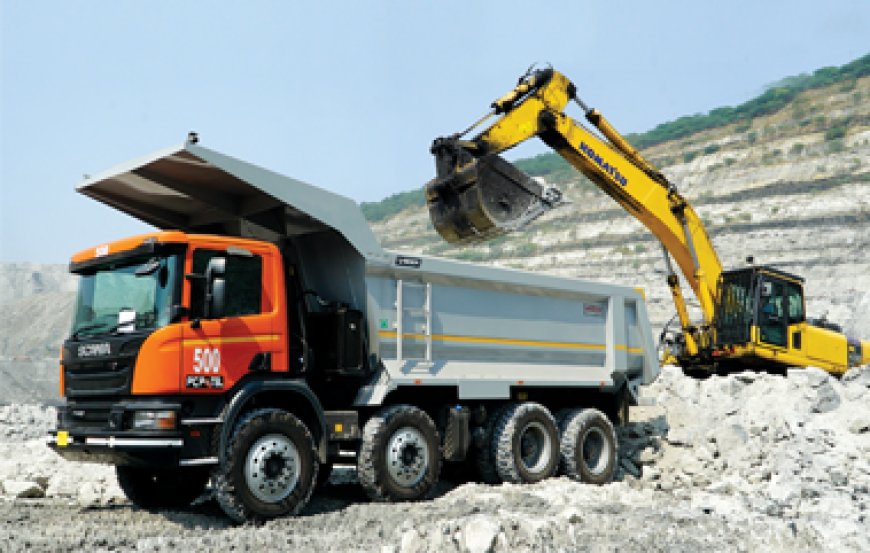
Komatsu’s ‘Komtrax’ uses satellite-based information communication technology (ICT) to provide constant monitoring of every machine.
Arun Pai,
General Manager-Product Support,
Larsen & Toubro Limited.
L&T has state-of the-art service centres at 6 locations fully equipped to carry out complete overhaul of equipment and its components as per the exacting standards of Komatsu, backed by a network of 30 dealers with over 130 outlets to provide door-step services to their customers. “We are in process of developing service mobility solutions for service team as well as customers,” states Arun Pai, General Manager-Product Support, Larsen & Toubro Limited. Pai highlights the core strengths and competencies of the company’s service capabilities.
How do you envision the changing dynamics of service industry in the CE space and how innovatively Komatsu / L&Thas transformed itself to address the challenges?
The CE customers expect equipment to be fitted with performance / health monitoring systems which would help them optimize the utilization of the machines as well as reduce maintenance per hour costs by carrying out timely preventive maintenance activities. Komatsu’s ‘Komtrax’ which uses satellite-based information communication technology (ICT) to provide constant monitoring of every machine, including operational conditions and status to help increase machine safety, productivity, uptime and availability – and reduce customers’ costs per tonne and per hour. L&T is in the process of digitalization of their parts and service operations, in sync with the Komtrax system including a 24×7 Helpline ‘EquipCare’ so that the customer service experience is enhanced.
A machine’s productive lifecycle is determined by the life of its major components. How do you ensure the same? Also elaborate on the Rebuild and Refurbishment services provided?
Komatsu has designed their CE to give a very high initial life of the major components, which reduces the hourly cost of maintaining the equipment over the lifecycle of the equipment. The health of the equipment as well as the major components are closely monitored by L&T’s wide network of dealer service engineers who carry out periodic Preventive Maintenance checks of these components and recommend to customers the timely repair action that is required.
L&T has state-of the-art service centres at 6 locations fully equipped to carry out complete overhaul of equipment and its components as per the exacting standards of Komatsu, backed by a network of 30 dealers with over 130 outlets to provide door-step services to their customers. L&T also has a Rebuilt Assembly Exchange Programme where ready to use Recon / Rebuilt components are offered at economical prices to customers on exchange basis along with repair warranty terms, which contains the equipmentdowntime substantially.
What are the major challenges in this, especially when a dispute arises? What are the dispute resolution mechanisms available, and how fast it is taken care of?
A major challenge is the presence of local workshops and traders selling non-genuine parts at lower prices, which lowers the cost of the component repairs, wherein the reliability is compromised. Knowledgeable customers will always opt for the genuine parts and rebuilt components offered by L&T, because they realize that in the long run, due to the much longer life of their rebuilt components, the maintenance cost per hour is much lower.
Designing service products depends on customer-focused metrics such as machine uptime and concepts such as MTR (mean time response), MTTR (mean time to repair) and MTBF (mean time between two failures). How innovative your strategies are in these areas?
As mentioned, the digitalization of L&T’s operations, including the 24×7 helpline EquipCare will result in further reduction of the MTTR (response) & MTTR (Restore) from the existing levels. MTBF depends on product reliability; Komatsu CE is already rated as amongst the most reliable in the industry. L&T’s digitalization programme will further improve the quality and speed of reporting of product related issues, which will help Komatsu reduce the time-span for taking corrective action.
What has been the impact of data driven technologies while Komatsu / L&T designing aftermarket support systems?
With the data available through Komtrax, the performance parameters have been studied and based on this, the extended warranty /Suraksha scheme has been offered to customer for 20T excavator as a first step.
What do you expect the next stage of such innovations based on big data analytics in the service industry? Are you developing any new such solutions?
After the implementation of 24×7 helpline, EquipCare across pan India, we are in process of developing service mobility solutions for service team as well as customers. Through this facility our service team will be able to give the equipment condition report as well as parts quotation/availibity to the customer instantly thru app-based applications in mobile.
Could you throw some light on your after-sales service portfolio?
L&T has 6 service centres pan-India, a world class training centre at Kanchipuram that is rated by Komatsu as amongst the best of their distributors world-wide and a network of 30 dealers with over 130 outlets, supported by a central warehouse located at Nagpur with a huge inventory and a ‘First Pick Efficiency of over 95%. All service centres have highly trained and skilled service engineers with high quality facilities for repair and testing of Komatsu components, including a robust Rebuilt Exchange Programme. For the Komatsu and Scania range of mining equipment, L&T has over 100 sites at various customer locations providing 24 x 7 support under Full Maintenance Contract and Site Support Agreement programmes.
Our Central Training Centre at Kanchipuram and the 4 regional training centres are all accredited to the National Skill Development Council / Infrastructure Equipment Skill Council, both affiliated to the PMKVY programme, to provide extensive operator and mechanic training support to our customers (both at the training centres and customer sites), apart from our regular internal training programmes.
What are the major after market challenges you face in terms of quality and availability of skilled technicians / workforce and other areas?
Due to the higher aspirational levels of the youth of our country, a few people – especially in the large metros – want to work as technicians in our industry. However, the demand for skilled technicians and service engineers in our industry is huge – hence the youth who opt for this career are guaranteed immediate employment upon completion of their training. We are aggressively promoting the career of a service engineer / technician in schools, ITIs, polytechnics and various other for a with a fair degree of success. Today, the brand value of a person who has been trained by L&T is the highest in our industry.
Your views on the Bauma Conexpo India 2018? Please also throw some light on the new launches?
Bauma Conexpo is an important exhibition on infrastructure industry and provides a platform to showcase technology updates and new products in construction equipment and material handling segment. Potential buyers especially from northern and westernIndia are eager to visit the exposition to scout for efficient machines that provide reliable performance and more profitability. BC India is growing in size and stature and today attracts many players offering a variety of products and services. There are many custom-made products that are India-specific. Buyer-Seller meets provide good leads in business and help the customers to expand business operations.
Larsen & Toubro is exhibiting 15 machines in its outdoor stall in BC India. Komatsu’s new line of machines in 30T class, PC300LC-8M0 and PC350LC-8M0 hydraulic excavators will be launched which will have a big market in stone, quarry and marble industry. Besides, L&T is displaying its new line of products for the road construction sector, such as L&T hydraulic paver, pneumatic tyred handler and skid steer loader.
Hits: 317