Calls for certified Workforce Gains Momentum for Progressive Work Environment
As merely 5-6% of the construction equipment and mining equipment operators are certified skilled operators, the cry for certification and skilling the unskilled operators has gained momentum in recent years. Industry bodies and companies have demanded government to incentivise the
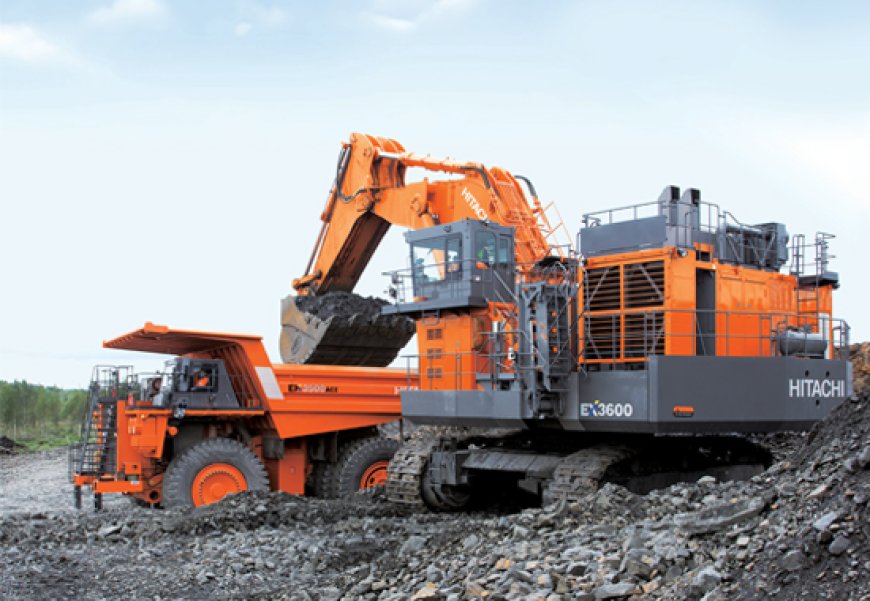
As merely 5-6% of the construction equipment and mining equipment operators are certified skilled operators, the cry for certification and skilling the unskilled operators has gained momentum in recent years. Industry bodies and companies have demanded government to incentivise the industry players who take up certification and training in big way, while making certification mandatory at the tender stage itself.
India will require an investment of over $1.5 trillion to modernise its infrastructure and related sector over the next five years. However, what cannot be ignored along with investments is the role of labour force – both skilled and unskilled to achieve the desired objective.
A major component of this development is the construction and the construction equipment sector. The sector employs around 3.6 crore workforce — between level 1 (primary) to level 7 (highly skilled) which will grow up to 4.73 crore by 2022.
The scope of the article however is the requirement of skilled workforce within the construction and mining equipment sector.
According to a study by Indian Construction equipment manufacturing association, the direct employment by construction equipment sector is over a million (10 lakhs), however the indirect employment is more than double, and if we include the associated and related industry players such as repairs, spares and construction workers the impact is around 10 times.
The prime association related to the sector believes there is shortage of certified skilled workers such as operators, mechanics and supervisors in the country which can be bridged only if government makes certification mandatory as policy for selection at the tender stage itself.
This has been one of the serious challenges for the industry. The industry provides employment to more than 830,000 operators and mechanics, who have largely been trained by Original Equipment Manufacturers (OEMs), and through on the job training programmes over the years. Given that most workers in this sector would be primary earners for the family, this in addition to the associated impact on other allied sectors (repair shops, small scale manufacture, construction workers, etc.), the overall impact would approximately be ten times of direct employment levels in the construction equipment sector.
There is potential for a 15% growth in direct employment over the next 4-5 years. With improving technology and higher emphasis on safety, there is wide spread requirement for training institutes which could cater to skilling needs through a structured program including certification.
The industry association (ICEMA) along with National Skill Development Corporation (NSDC) and CII have instituted a Skill development program to cater to this need. The Infrastructure Equipment Skill Council (IESC) has already instituted 19 job roles for 8 products with another 20 more products on the anvil.
Skilling the Mining Sector Employees
Similarly, with technological advancements, the skill set of the existing mining employees would require sufficient skill up-gradation. The mining organizations would benefit from training the existing employees to work as multidisciplinary professionals.
While mining industry employs 0.5% of India’s workforce of 47 crore in 2011-12 that is around 23.3 lakh people. This includes employment in the public and private establishments that is organized sector and employment in the unorganized sector including self-employment. The total employment in the mineral extraction segment, which employs the operators of excavators and backhoe loaders, alone, is 20.7 lakh people.
Lack of skilled labour: There are few government incentives to build a skilled workforce within the construction equipment market. Major construction equipment companies have to resort to establishing costly training centres to upgrade the skills of their workers.
The private sector companies have undertaken several activities to train and skill the workforce for the construction equipment and mining equipment sector.
Prominent among them that ET could speak to are: Tata Hitachi, CASE India and JCB.
Tata Hitachi:
Tata Hitachi understands the need of trained and skilled operators to operate high value equipments. The company conducts training programmes for maintenance staff and engineers customized as per ‘their requirements. Additionally, there are standard training programmes organized throughout the year for which the schedules are shared with the customers.
For equipment operators, there are two type of training programs: Hands on training on equipment. Training on Simulator. Training on Simulator: The company has setup a simulator-based training facility for operators at the Dharwad and Kharagpur Training Centers. These offer the latest in simulator training.
There are two courses offered for Simulator training – Excavator Module. Dump Truck Module.
Training on Equipment
Dharwad and Kharagpur have two training centers where operators are trained on machines.
Both the training centers impart operating and servicing to unemployed youth to enhance their employability as operators for the construction equipment industry. The training centers have multiple classrooms supported by electronic and visual aids in addition to machines for practical sessions for imparting world-class training. The program includes theory on equipment, practical and hands on training for aggregates.
CASE India:
Lack of skilled workforce and inefficient trainees have always been a concern in manufacturing industry. Skilled workforce with proper training is the need for progressive work environment.
For a skilled labour force we would require dedicated training centres that hosts training programmes to make operators understand the machine mechanism, operations and get familiar with technical factors.
At CASE India, we have training centres that host training programs all-round the year for operators and customers to constantly keep them updated with latest practices and techniques. We deal with skilled manpower development or skilling the manpower with a multipronged approach. First approach is to train the operator. We have an operator training school which brings in unemployed youth. They are given hands-on training and understanding of the machines and its application in a better way.
The second approach is for heavy line machines like Graders and dozers, which are more technological, more sophisticated and need specialized operator. Here we provide trained operators to the customers and try to bridge the skill gap. The third approach is about design change in the machines. Design change is a way that makes it easy for even a semi-skilled operator to run the machine. The machines are designed in such a way that even a semi-skilled operator can easily make out the critical parameters and coordinates of the machine.
JCB has So far trained more than 25,000 people. And many of their centres are accredited to the Infrastructure Equipment Skill Council (IESC), some of which are also linked to Pradhan Mantri Kaushal Vikas Yojana (PMKVY). “We have pioneered this segment with the first centre established almost 15 years ago,” said Jasmeet Singh, AVP – Corporate Communications JCB India.
HS Mohan, CEO, Infrastructure Equipment Skill Council, believes spilling the workforce has direct correlation to efficiency and improved lead times. “When we skill the workforce the efficiency and lead times improve, while it has a direct bearing on keeping a check on project cost over runs.”
The best strategy to improve standardisation in skill sets is by certifying the workforce. It will increase their employability not just in India but even abroad.
“Government needs to encourage employment of skilled and certified personnel. All National Highway & State Highway tenders needs to mandate deployment of skilled and certified operators. If need be, the industry needs to be incentivised in the form of tax concessios. Even Finance & Insurance companies should insist on certified personnel operating the costly machines,” Mohan said.
Hits: 233