The government needs to make it mandatory to employee only skill-certified operators.
Anand Sundaresan, Vice-Chairman & Managing Director, SchwingStetter India as – Chairman of the IESC. The Infrastructure Equipment Skill Council (IESC), promoted by the Indian Construction Equipment Manufacturers Association (ICEMA), subsidized by the National Skill Development Corporation (NSDC) appointed Anand Sundaresan,
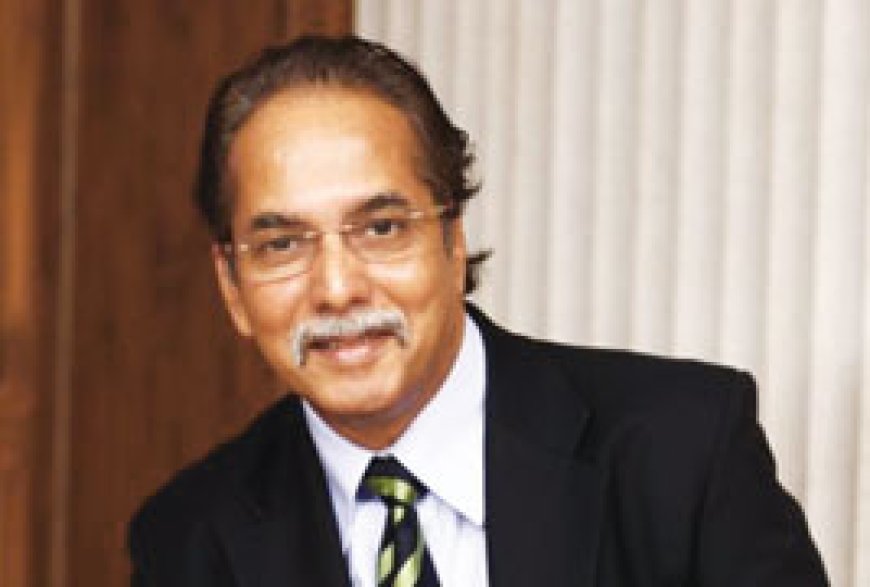
Anand Sundaresan,
Vice-Chairman & Managing Director,
SchwingStetter India as – Chairman of the IESC.
The Infrastructure Equipment Skill Council (IESC), promoted by the Indian Construction Equipment Manufacturers Association (ICEMA), subsidized by the National Skill Development Corporation (NSDC) appointed Anand Sundaresan, Vice-Chairman & Managing Director, Schwing Stetter India as – Chairman of the IESC at the 11th Governing Body Meeting held recently. “In India, we have always had a deficit in manpower especially in the infrastructure and construction industry. As the government has been focusing on introducing and implementing policy reforms that will create huge employment opportunities.” In a freewheeling chat Sundaresan shares the road map of IESC with EQUIPMENT TIMES.
Taken charge as the new Chairman of IESC, what is your road map for the years 2017-19?
The IESC has, over the past three years, done a commendable job in both establishing a strong foundation and also building the basic framework for the skill eco system in the industry. Our next step is to scale up operations by increasing our foot prints across the country covering all the states and select districts within them, which has the inherent potential for mobilization and opportunities for placements.
These training centers would be established utilizing the existing assets such as of ITIs & other Institutes with financial support from the government and technical assistance from the Industry/OEMs. The ownership of these will vest with private players in the skilling space who have the not only the competency but also the passion and commitment to deliver.
Concurrently we hope to make the CEMM Act a reality which will be a game changer in the industry. And till such time our efforts will be to bring the vast pool of experienced operators but not formally certified into our fold through the RPL model (Recognition of Prior Learning) We plan to rope in all the stake holders primarily the end users through their apex bodies like Builders Association of India and Crane Owners Association to name a few.
What are the challenges you anticipate and how you prepare to iron out the issues?
The major challenges are primarily the jobs roles of operators and mechanics to an extent being non-aspirational; and no visible demand for certified operators. With the CEMM Act getting approved or till such time an interim government mandate for certified /licensed operators only to ‘man’ the machines backed up by an effective monitoring system; the demand for skilled operators will rise exponentially.
Is there any reliable statistics on the demand-supply scenario of skilled manpower, specifically for the operators and technicians for construction and mining equipment?
In the infrastructure equipment sector close to 60% is in the unorganized segment and hence getting the exact or ‘close enough’ figures has always been a challenge. How-ever based on the sales data of machines by OEMs we are able to get a fair idea of the demand supply scenario. Thus the projected demand, after factoring in other variables, is generally in line with the industry growth. However, a point to be noted here is that, most of the operators are skilled or trained on the job, provided by the OEMs at time of commissioning the equipment, and get trained over a period of time. Most of them are certified by the OEMS and not by the sector skill council.
Give us an overview of the skill development initiatives undertaken by IESC?
Development of National Occupational Standards (NOS) and Qualification Packs (QPs). A total of 33 nos covering nearly 80% of the workforce in the industry approved. Another 10 nos are in the pipeline to bridge the gap and enable career progression. Accreditation of around 50 training partners pan India; majority being OEM / OEM supported followed by certification of trainers around 200. This enabled us to train approximately 3500 personnel to date. CII (Confederation of Indian Industry) is our Assessment Agency to bring value and repute to the IESC certificates.
MOUs with several State Skill Development Missions, AICTE Colleges, PSUs like Coal India etc, central organizations like NHIDCL and NHAI to drive the skilling projects forward. Besides Indian Army for capitalizing on their vast trained and retiring manpower.
The target of IESC was to train about 20 lakh people since its inception. Where have we reached?
To understand our growth in the correct perspective it is essential to know the background. In 2010 we were selling close to 60,000 machines and it was expected to touch 300,000 machines over the next decade. This entailed a demand of nearly 20 lakh operators and mechanics.
Keeping this projected requirement in mind it was proposed to form the skill council to spearhead this skilling initiative. How-ever by the time this took shape in 2014 the industry was passing through a slump from which it has just started recovering.
Hence the original targets are unrealistic in the present context and are under review. We have so far trained around 3500 personnel through 50 odd Training Partners and around 200 Certified Trainers.
The major challenges are primarily the jobs roles of operators and mechanics to an extent being non-aspirational; and no visible demand for certified operators. Both these combine to make mobilization a daunting task!!
How do you plan to incorporate various stakeholders specifically for formulating the syllabus for the training programs?
In the first step all the stake holders mentioned above were fully involved in the development of standards (NOS & QPs). They not only supported us during the field study but also helped us validate these before submission to the Government for approval.
These standards encompass not only the performance criteria but also the assessment norms. The training curriculum and programs evolve naturally from this. Also these standards are due for revision every two years wherein the feedback from all the stake holders are obtained and examined.
How does ICEMA intend being a bridge between these various stakeholders?
As per our MOA (Memorandum of Association) only ICEMA members can be members of IESC. Currently we have 29 members and going forward we hope to increase our fold. ICEMA has been publicizing and supporting at all forums the pioneering efforts of IESC in transforming the skill landscape in the industry.
What do you think the role of dealers of different OEMs and how IESC catalyze their support in achieving the target?
The dealers of the OEMs form a very critical link in the skill eco system as they are the interface between the manufacturers and end users. In order to increase our touch points IESC has been affiliating select and competent dealers as our training partners.
It is not mandatory to employ certified operators to operate the construction equipment. What is your take on this and also spell out your plans to ensure only trained operators operates the machine?
This is the crux of the whole matter and unless it is mandated as in most of the other countries mobilization will be a challenge and more-so considering jobs are not readily and visibly forthcoming at present. It is hoped that once the CEMM Act comes into force this will be taken care of. Besides IESC is working in close tandem with equipment insurance and financing companies to offer incentive schemes to machine owners employing IESC certified personnel only.
How will ICEMA ensure the operators are regularly trained to handle new or upgraded rollouts?
As a first step, when new models enter the field OEMs train the end users through their dealers at the time of installation/commissioning. Moving forward we are in the process of working out a system whereby all OEMs keep IESC in the loop of such technological developments. IESC in turn will inform all their Training Partners on a regularly basis through TNB (Training News Bulletins)
Would you consider training on a commercial basis? How the stakeholders are pitching in?
In view of the high capex and opex involved in establishing and operating a Training Centre for training of operators and mechanics on infrastructure equipment; other than OEMs very few third party / private organizations are willing to take it up due to financial viability.
As of now students are not willing to bear even part of the cost as they do not see any visible demand for skilled operators currently. At the same time they are willing to pay any amount provided they get a job immediately thereafter. Hence the commercial model will have to wait till the job situation improves.
The North East and rural areas have emerged as a big opportunity for road building equipment manufacturers. What are the steps being taken by ICEMA to cater to these areas?
IESC has signed an MOU with NHIDCL (National Highway Infrastructure Development Corporation Ltd) for skilling of operators employed on their road projects in the North East and the programs have since kicked off.
Select OEMs are conducting this training through their Local Dealers and Regional Training Centers which are affiliated to IESC. Moving forward IESC is also considering establishment of a regional office at Kolkata /Guwahati once the momentum picks up.
Further IESC is collaborating with NHAI (National Highways Authority of India) to establish Model Training Centers pan India to support the training and certification of operators involved in highway construction projects. A preliminary proposal submitted by IESC is under active consideration.
Hits: 28