Our R&D team has augmented our product design to reduce fuel consumption across all the equipment.
Do you offer customization options for your concrete equipment to meet specific client requirements? Yes, we offer customization options for our concrete equipment to meet specific client requirements. We have a dedicated team of engineers and product designers who are
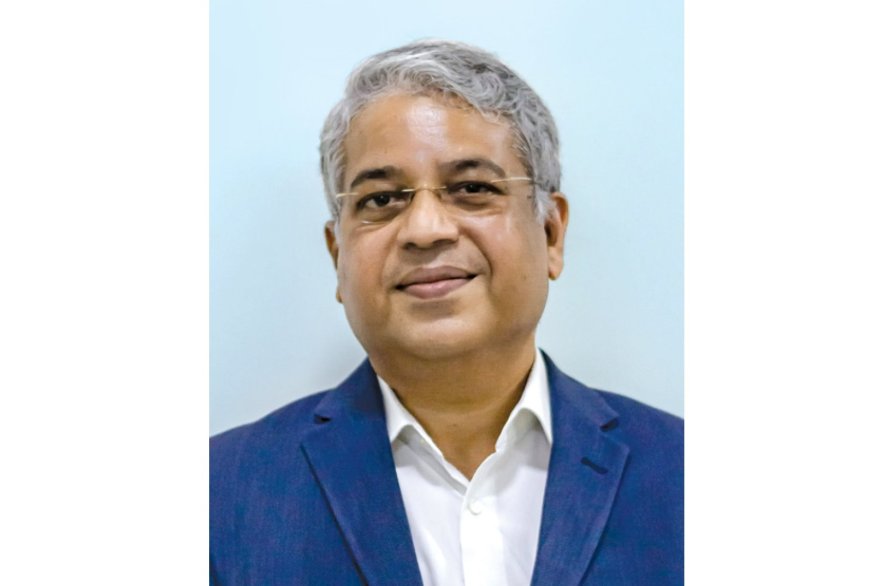
Do you offer customization options for your concrete equipment to meet specific client requirements?
Yes, we offer customization options for our concrete equipment to meet specific client requirements. We have a dedicated team of engineers and product designers who are specialists in understanding the requirements and providing the best solutions for your project. Whether you need a special configuration, a higher capacity, or a unique feature, we can customize our equipment to suit your preferences.
What quality standards do you adhere to during the manufacturing process? How do you ensure the equipment is built to withstand harsh environments & prolonged use?
We adhere to the highest quality standards during the manufacturing process of our concrete equipment. We use only the best materials and components, and we follow strict quality control procedures at every stage of production. We also conduct rigorous testing and inspection of our equipment before delivery to ensure it is built to withstand harsh environments and prolonged use.
How do you ensure the durability, reliability, and performance of your concrete equipment?
We ensure the durability, reliability, and performance of our concrete equipment by using innovative technology and design features. For example, our easy mode in boom pumps and single side pumping of concrete are some of the unique features of SCHWING products. The spirals in our concrete mixer are technologically designed to give better homogeneity mix and higher strength mix. With our passion for innovation, our concreting products are dominant in the Indian CE market.
How do you handle repairs, servicing, and spare parts availability?
SCHWING Stetter has always been associated with its after-sales support excellence, be it service, spares, or training requirements. With close to 26 Branches pan India, and 12 Service centers and as many Spares depots, SCHWING Stetter provides direct and immediate service to its customers. The Service centers provide Overhauling/refurbishment of equipment with limited warranty. Scheduled Health Check-up of all RMC Plants and Audit of Operators periodically have garnered huge appreciation from the clients. Apart from this, the resident service engineers take care of clustered equipment in remote areas. We also stock up
Do you offer technical support for operating and maintaining the equipment?
Yes, we offer technical support for operating and maintaining the equipment. We provide training and manuals for our customers on how to use and maintain our equipment safely and efficiently. Our pan-India wide network of service engineers are ready to offer any required on-site support promptly without any delays.
Are there any energy-efficient or eco-friendly features incorporated into your concrete equipment?
Our R&D team has augmented our product design to reduce fuel consumption across all the equipment. Our batching plants are designed for faster erection and easy maintenance, which saves time and resources. Our in-house automation helps us meet the requirements of the customers in terms of CRM and IOT and tailor-made solutions for customer need.
Are you working on any new developments or improvements in your concrete equipment lineup?
Yes, we are working on some new developments or improvements in our concrete and construction equipment line-up. With our R&D centre in place, SCHWING Stetter India will be unveiling a slew of newer technology equipment with higher capacities in our range of products will be unveiled during the upcoming expos.
Have you worked on any notable projects that required customized equipment solutions?
We have worked on some notable projects that required customized equipment solutions. Our equipment was part of the construction of the Statue of Unity in Gujarat, which is the world’s tallest statue. We also supplied batching plants and other machines for the construction of the Chenab Bridge in Jammu and Kashmir, which is the world’s highest railway bridge. With the completion of 25 years in the Indian CE industry in 2023, SCHWING Stetter India has generated a brand identity that ensures that our equipment are a must have for any large scale projects happening in India.
Hits: 4