L&T’s fully indigenously manufactured range of road machinery have been successfully deployed in various projects under Bharatmala.
Vivek Hajela VP, CEB, Larsen & Toubro How do you perceive the opportunities getting better for the OEMs in the construction equipment industry as the Bharatmala project aims to ensure speeding up approval
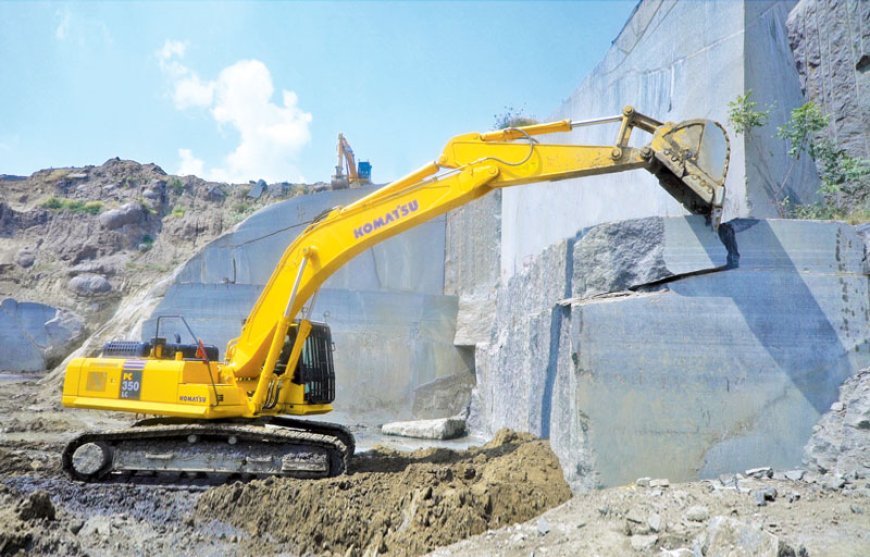
How do you perceive the opportunities getting better for the OEMs in the construction equipment industry as the Bharatmala project aims to ensure speeding up approval processes to enable quicker execution of projects?
The Ministry of Road Transport and Highways (MoRTH) has made significant progress under the PM Gati Shakti National Master Plan in improving multi-modal and last-mile connectivity across India. The PM Gati Shakti National Master Plan involves developing 22 greenfield expressways, 23 major infrastructure and highway projects, and 35 Multi-Modal Logistics Parks (MMLPs) as part of the ministry’s Bharatmala Pariyojana, at an estimated investment of Rs 5.35 lakh crore.
MoRTH has already increased the speed of implementation of 35 MMLP projects under the Bharatmala Pariyojana Phase I through its implementing agencies NHAI, NHLML and NHIDCL. For example, a Multi-Modal Logistics Park at Jogighopa, Assam, is already under construction. In addition, the Government has already invited bids for four MMLPs in Nagpur, Chennai, Bengaluru and Tamil Nadu.
Moreover, important corridors and projects under construction are Delhi – Mumbai Expressway, Delhi – Amritsar – Katra Expressway, Ahmedabad – Dholera Expressway, Bengaluru – Chennai Expressway, Amritsar – Bhatinda – Jamnagar Expressway, Raipur – Vizag Expressway, Ambala – Kotputli Expressway, Hyderabad – Vizag Expressway, Chennai – Salem Expressway and Chittor – Thatchur Expressway.
Some of the significant key infra projects under construction are Zojila Tunnel (Ladakh), roads to connect Krishnapatnam Port in Andhra Pradesh, the widening of Lalpul-Manmao changing road in Arunachal Pradesh, a bridge over Middle Strait Creek in Andaman and Nicobar Islands, 6-lane bridge over Ganga bridge at Phaphamau in Uttar Pradesh and a 4-lane bridge over river Brahmaputra between Dhubri-Phulbari in Meghalaya.
The Government’s initiative of implementing a host of projects throughout the country will lead to a substantial increase in demand for Construction Equipment (CE) in the days to come. We believe it will create immense opportunities for all players in the sector, including L&T Construction and Mining Machinery, which has always pioneered in the introduction of cutting-edge technologies revolutionising the industry over the years.
In fact, against degrowth in the previous fiscal, the CE sector is expected to register positive growth in the current financial year. Moreover, the growth rate will gradually rise as the projects undertaken by the Government picks momentum.
How do you see initiatives like the ‘Make in India’ PLI scheme further accelerating the growth of the construction equipment sector?
The Government’s initiatives of ‘Make in India’ and PLI, combined with projects like PM Gati Shakti National Master Plan, and BharatmalaPariyojana, will boost the CE sector in several ways.
As infrastructure projects gain momentum, demand for CE will substantially increase, expanding the market. In addition, it will create opportunities for economies of scale for CE production in India and prompt original equipment manufacturers (OEMs) to invest in greenfield or brownfield capacity expansion. CE manufacturers will thus gain from the PLI scheme, which provides companies with incentives for incremental sales from products manufactured in domestic units.
Furthermore, the Make in India PLI scheme will facilitate CE production because it aims to promote investment, encourage innovation and create state-of-art manufacturing infrastructure.
Additionally, as economies of scale kick in, the PLI scheme will attract global component manufacturers to set up shops in India and motivate existing OEMs to expand capacities to cater to export demand.
Which of your equipment are employed in the Bharatmala project? What are your major contributions to this project?
Our customers have employed a large number of machines from Komatsu and L&T at various locations for road and infrastructure projects undertaken by the Government under various schemes and projects. We offer a wide range to Komatsu’s excavators to our esteemed customers and have supplied large volumes of PC71, PC130, PC210-10M0 and PC300-8/PC350-8 excavator models for road construction.
Komatsu PC210-10M0 Hydraulic Excavator, launched at the last EXCON held in Nov’2019, has been received exceptionally well. It has set new performance benchmarks and is set to become a game-changer for the industry. We have already sold 2000 machines, and many of them have clocked 10,000 hours of satisfactory performance. Therefore, we see this machine emerge soon as an undisputed leader in the 21-ton segment.
L&T’s own fully indigenously manufactured range of road machinery such as Vibratory Compactors, Wheel Loaders and Pneumatic Tyres Rollers have also been successfully deployed in various projects under Bharatmala etc. These machines have helped enhance the pace of work with their reliable and durable performance.
Last mile connectivity is crucial. How do you assess the challenges in the Bharatmala project in terms of construction equipment?
As many last or first-mile connectivity projects are to be constructed in remote areas, mobilising equipment and raw materials could be challenging for many players. However, L&T Construction & Mining Machinery, with a 75-year experience in after-sales, have developed the expertise to support equipment at every location in the country-remote or accessible.
The machines we deal with are equipped with the latest technology, and we combine world-class after-sales support with them, including Full Maintenance Contracts and Annual Maintenance Contracts. Our state-of-the-art after-sales service delivery makes sure customers can keep their machines running so that per unit of production cost is minimised and productivity maximised, providing better returns on investments.
In addition, customers can remotely monitor every piece of equipment’s health. It helps them avoid failures and reduce maintenance costs since the cost incurred in rejuvenating a failed engine is much higher than the cost of an in-time proactive rehabilitation of a component.
Hits: 1