Unearthing Tomorrow India’s Sustainable Mining Transformation
The mining industry has always been at the forefront of technological innovation, driven by the relentless demand for minerals, metals, and resources that power our modern world. From the early days of pickaxes and shovels to the sophisticated machinery of today, the evolution of mining equipment has been nothing short of transformative.
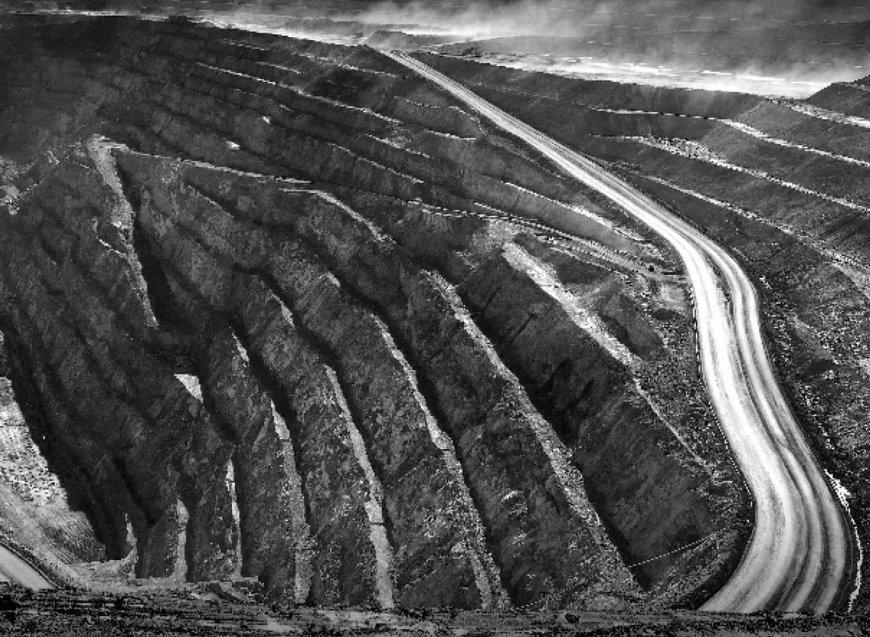
The mining industry has always been at the forefront of technological innovation, driven by the relentless demand for minerals, metals, and resources that power our modern world. From the early days of pickaxes and shovels to the sophisticated machinery of today, the evolution of mining equipment has been nothing short of transformative. In recent years, the integration of advanced construction equipment into mining operations has revolutionized the industry, enhancing efficiency, safety, and sustainability.
Equipment Times explores the evolving mining industry, key trends, advancements in mining equipment technology, digitalization and automation transforming mining operations, primary challenges, emerging markets or new applications, key expectations of mining companies, reliability, safety, and cost-efficiency of mining equipment.
Mining and construction have always shared a symbiotic relationship. Many of the machines used in construction—excavators, bulldozers, loaders, and dump trucks—are also essential in mining operations. However, the demands of mining are unique, requiring equipment that can withstand extreme conditions, handle massive loads, and operate efficiently in remote and often harsh environments.
Today, mining-specific versions of construction equipment are designed to meet these challenges head-on. These machines are built with reinforced structures, advanced hydraulic systems, and powerful engines that enable them to perform in the most demanding mining environments. For example, hydraulic excavators used in mining are often equipped with larger buckets and longer arms to reach deeper into the earth, while mining trucks are designed to carry payloads of several hundred tons.
The Future of Mining - Automation and Robotics
One of the most significant advancements in mining equipment is the integration of automation and robotics. Autonomous haul trucks, drilling rigs, and loaders are becoming increasingly common in mining operations around the world. These machines are equipped with advanced sensors, GPS technology, and artificial intelligence (AI) that allow them to operate with minimal human intervention.
Autonomous mining equipment offers several advantages. First, it improves safety by reducing the need for human operators to work in hazardous conditions. Second, it enhances efficiency by operating 24/7 without the need for breaks or shift changes. Finally, it reduces operational costs by optimizing fuel consumption and minimizing wear and tear on equipment.
For example, Rio Tinto, one of the world’s largest mining companies, has implemented a fully autonomous haulage system at its Pilbara iron ore mines in Australia. The company’s fleet of autonomous trucks has travelled millions of kilometres, moving millions of tons of material with remarkable precision and efficiency. This level of automation is a testament to the potential of advanced construction equipment in revolutionizing the mining industry.
Sustainability and Environmental Considerations
As the global focus on sustainability intensifies, the mining industry is under increasing pressure to minimize its environmental impact. Advanced construction equipment is playing a crucial role in helping mining companies achieve their sustainability goals.
Electric and hybrid mining equipment is becoming more prevalent, offering a cleaner alternative to traditional diesel-powered machines. Electric excavators, loaders, and trucks produce zero emissions at the point of use, reducing the carbon footprint of mining operations. Additionally, regenerative braking systems in electric vehicles can capture and reuse energy, further enhancing their efficiency.
Moreover, advanced equipment is enabling more precise and targeted mining, reducing the amount of waste generated and minimizing the disturbance to the surrounding environment. For example, precision drilling technology allows miners to extract ore with greater accuracy, reducing the need for excessive excavation and lowering the environmental impact.
The Indian Mining Market’s Growth, Challenges, and Technological Transformation
India’s mining sector, a cornerstone of its industrial and economic growth, is undergoing a seismic shift. Fuelled by rising domestic demand for minerals, government-led reforms, and a push toward sustainable practices, the Indian mining market is poised to become a global powerhouse. As the world’s third-largest coal producer and a significant player in iron ore, bauxite, and rare earth minerals, India’s mining industry is not only critical for its own infrastructure development but also increasingly vital to global supply chains. Here’s a closer look at the dynamics shaping this rapidly evolving sector.
India’s Mining Landscape: A Snapshot
India boasts a vast mineral wealth, with over 1,500 operational mines producing 95 key minerals, including coal (44% of total mineral production), iron ore, bauxite, limestone, and manganese. The sector contributes approximately 2.5% to India’s GDP and employs over 1.1 million people directly. Key states like Odisha, Chhattisgarh, Jharkhand, and Rajasthan are mineral-rich hubs, driving both domestic consumption and exports.
However, despite its potential, India’s mining sector has historically faced challenges such as bureaucratic delays, environmental concerns, and outdated infrastructure. In recent years, the government has prioritized reforms to unlock this potential, positioning mining as a linchpin of India’s ambition to become a $5 trillion economy.
Policy Reforms: Accelerating Growth
The Indian government has introduced landmark reforms to attract investment, streamline operations, and promote transparency:
Mines and Minerals (Development and Regulation) Amendment Act (2021): Removed restrictions on end-use of mined minerals, allowing commercial mining of coal and other minerals.
Introduced a transparent auction process for mining leases, reducing monopolies and encouraging private participation.
National Mineral Policy (2019): Focuses on sustainable mining, technology adoption, and boosting exploration activities.
Aims to increase the mining sector’s contribution to GDP to 4% by 2030.
Aatmanirbhar Bharat (Self-Reliant India): Prioritizes domestic coal production to reduce reliance on imports (India imported 237 million tonnes of coal in FY23).
These reforms have already borne fruit. For instance, the auction of 87 coal blocks since 2020 has attracted major players like Adani, Vedanta, and Tata Steel, while Coal India Limited (CIL), the state-owned behemoth, aims to produce 1 billion tonnes of coal annually by 2025–26.
Construction Equipment in Indian Mining: Demand and Innovation
The surge in mining activity has driven demand for advanced construction and mining equipment. India’s construction equipment market, valued at $6.5 billion in 2023, is projected to grow at 6–8% annually, with mining equipment accounting for a significant share. Key trends include:
Rise of Heavy-Duty Machinery: Indian miners are increasingly adopting high-capacity dump trucks (100+ tonnes), hydraulic excavators, and drill rigs. Companies like BEML, Tata Hitachi, and JCB are expanding their portfolios to cater to mining-specific needs.
Electrification and Hybrid Solutions: To curb emissions and operational costs, electric and hybrid equipment is gaining traction. Tata Hitachi’s electric excavators and Eicher’s electric trucks are being piloted in smaller mines.
Digitalization and Automation: While full autonomy is still nascent, Indian miners are adopting telematics, IoT-enabled fleet management systems, and predictive maintenance tools. Companies like Sandvik and Epiroc are partnering with Indian firms to deploy autonomous drilling rigs and AI-driven analytics.
Challenges: Balancing Growth and Sustainability
Environmental and Social Concerns: Land acquisition disputes, deforestation, and water pollution remain contentious. The 2023 protests against bauxite mining in Odisha’s Niyamgiri hills underscore the need for community engagement.
Infrastructure Gaps: Poor road connectivity and rail networks in mining regions delay logistics and escalate costs.
Regulatory Complexity: Overlapping state and central laws, coupled with lengthy approval processes, deter investors.
Sustainability: A New Frontier
India’s mining sector is aligning with global ESG (Environmental, Social, Governance) goals:
Renewable Energy Integration: Mines are adopting solar power to reduce reliance on diesel. CIL plans to install 3 GW of solar capacity by 2025.
Mine Reclamation: Progressive closure policies ensure mined land is restored for agriculture or tourism. The Neyveli Lignite Corporation’s afforestation projects in Tamil Nadu are a model example.
Critical Minerals for Green Tech: India is ramping up exploration of lithium, cobalt, and rare earth elements to support electric vehicle and renewable energy industries.
The Indian mining market is no longer just digging deeper—it’s digging smarter. With supportive policies, technological leaps, and a renewed focus on sustainability, the sector is set to redefine its role in India’s growth story. For construction equipment manufacturers, this represents a golden opportunity to innovate and collaborate in one of the world’s most dynamic markets. As India unearths its mineral wealth responsibly, it is also laying the groundwork for a future where mining and sustainability coexist.
The Importance of Maintenance and Training
While advanced construction equipment offers numerous benefits, it also requires specialized maintenance and training to ensure optimal performance. Mining equipment is subjected to extreme conditions, including dust, heat, and heavy loads, which can lead to accelerated wear and tear. Regular maintenance is essential to prevent breakdowns and extend the lifespan of the equipment.
In addition, operators and maintenance personnel must be trained to handle the complexities of modern mining equipment. This includes understanding the advanced technologies and systems that power these machines, as well as adhering to strict safety protocols. Many equipment manufacturers offer comprehensive training programs to help mining companies get the most out of their investments.
The mining industry is undergoing a profound transformation, driven by the integration of advanced construction equipment. From autonomous haul trucks to electric excavators, these machines are enhancing efficiency, safety, and sustainability in mining operations around the world. As technology continues to evolve, the potential for further innovation in mining equipment is virtually limitless.
For mining companies, staying ahead of the curve means embracing these advancements and investing in the latest equipment and technologies. By doing so, they can not only improve their operational efficiency but also contribute to a more sustainable and responsible mining industry. The future of mining is here, and it is being built by the cutting-edge construction equipment that powers it.
For construction equipment providers, the message is clear: India’s mining revolution is just beginning, and those who invest in cutting-edge, eco-friendly solutions today will reap the rewards tomorrow.
Industry voices…
Dimitrov Krishnan, Managing Director, Volvo Construction Equipment - India Business & Chairperson, Infrastructure Equipment Sector Council (IESC), said, “The mining industry is undergoing a significant shift, driven by technology, sustainability, and evolving global demand. The adoption of automation technologies and digital tools will enhance operational efficiency and safety. Companies will increasingly utilize remote-controlled equipment, drones for surveying, and data analytics to optimize mining processes and reduce costs. Sustainability will also take center stage, with stricter environmental regulations pushing the industry toward low-emission and electric equipment. Additionally, the demand for minerals like lithium, cobalt, and iron ore is increasing as industries worldwide transition to greener energy.”
Joydeep Dasgupta, Director (Production), NMDC, said, “The mining sector is entering a transformative era, both in India and globally, as it adapts to meet the demands of a rapidly changing world. Historically, mining has been the backbone of industrial progress, providing materials essential for infrastructure development. Today, as the world shifts toward clean energy and sustainability, the sector is going to play a critical role in the transition. In India, the rapidly growing infrastructure sector is significantly driving the demand for steel, creating substantial opportunities in the mining industry as the need for raw materials like iron ore and coal continues to rise. One of the most significant opportunities lies in adopting sustainable mining practices, which focus on mitigating environmental impact while improving operational efficiency. Adoption of renewable energy sources to reduce the ecological footprints and digitalization and automation of production processes are transforming the mining sector, making it safer and more efficient. Further, the global transition to clean energy has created a surge in demand for strategic and critical minerals, positioning mining companies as key enablers of this transformation. Another pivotal dimension of the mining sector is the advancement in mineral exploration and extraction technologies. As traditional mining methods face challenges related to depleting high-grade ores and increasing environmental concerns, the mining companies can innovate and drive the development of technologies such as advanced geospatial mapping, seismic imaging, and remote sensing which enables more precise identification of mineral deposits, reducing exploration risks and operational costs.”
Sunil Gupta, COO, Vedanta Aluminium, said, “India’s mining sector is poised for significant transformation, driven by the increasing demand for critical minerals such as lithium, cobalt, and rare earth elements that are essential for the global energy transition. In addition, the country is on a rapid growth trajectory that makes it imperative to unlock wider access to essential minerals such as iron ore and bauxite to fuel the nation’s expanding requirements. India, with its vast mineral reserves, is uniquely positioned to meet both domestic and international demand. Regulatory reforms, such as the Mines and Minerals (Development and Regulation) Amendment Act, 2023, present added opportunities for private sector participation and exploration. Additionally, advancements in automation and digitisation offers potential for the sector to enhance productivity and safety. Sustainability remains a key driver, with the industry focusing on decarbonisation and responsible resource management to align with global ESG commitments.”
Dipankar Banerjee, Wholetime Director & Chief Executive Officer, Gainwell Engineering, “Gainwell Engineering manufactures room & pillar equipment for the underground mining industry, we believe the mining industry is poised for an exciting evolution over the next five years. This is primarily driven by a surge in demand for energy around the world and specially in emerging markets. Projections indicate that the global underground mining equipment market will reach approximately USD 28 billion by 2031, and we anticipate significant growth fuelled by industrialization and urbanization of economies in India, China, Indonesia, and others. The transition towards sustainable practices and the adoption of advanced technologies will further enhance operational efficiencies, creating a vibrant landscape for innovation and investment.
Large volumes of coal are needed for power generation in several regions across Asia, Africa and Australia. This includes China, Indonesia, India and even the United States to a certain extent where despite a decline in demand the overall volume of coal needed remains healthy. Additionally, electrification and automation in mining operations is also a key trend shaping demand. As companies strive to reduce emissions and improve safety, there is a growing emphasis on electric and hybrid machinery. Advancements in digital technologies such as IoT sensors and data analytics are revolutionizing operational efficiency, driving demand for modern equipment that can support these innovations.”
Anuj Keoliya, Senior Vice President - Surface Mining, GMMCO, said, “India is uniquely positioned to capitalize on its cost advantages in mineral production, driven by strong economic growth and increasing demand from core industries. With robust government policies, an expanding infrastructure sector, and a rising energy need, the demand for metals and minerals is set to surge.
As India moves toward its ambitious goal of a USD 5 trillion economy, mining will play a crucial role in meeting the demands of industrial expansion. Coal, iron ore, and other critical minerals will witness heightened exploration and extraction. Gmmco, with its deep-rooted expertise and commitment to delivering integrated solutions, is poised to support this growth with cutting-edge mining equipment, automation, and customer-centric services. Our strong network and industry insights place us at the forefront of India’s mining evolution. India’s mining industry is undergoing a significant shift, prioritizing safety, efficiency, and automation. Companies today are not just seeking machines—they are looking for sustainable, cost-effective solutions that ensure long-term productivity. At Gmmco, we understand that Total Cost of Ownership (TCO) is paramount for our customers.”
Kalpesh Desai, Managing Director, Gefran India, said, “In the next five years, the mining industry will experience significant growth in sustainability awareness, digitalization, and automation. The integration of cutting-edge technologies, such as smart sensors and automated control systems, will play a key role in increasing operational efficiency and reducing environmental impact.
The mining equipment industry faces several key challenges. One of the foremost is meeting increasingly stringent environmental regulations, which require significant innovation to reduce emissions and promote sustainable resource extraction while maintaining performance. High operating costs, driven by rising energy prices, raw material expenses, and labor, also exert pressure on mining companies, necessitating energy- efficient solutions to mitigate financial strain. Another challenge is the rapid pace of technological advancements, which demand continuous RCD investment to integrate automation and digitalization seamlessly into existing systems without compromising safety.”
Tarique Salman, Segment Manager – Specialty Excavation, Vermeer India, said, “The mining industry is expected to evolve in the next five years through the integration of new technologies, such as artificial intelligence (AI), digital twinning, and automation. These technologies are expected to improve safety, efficiency, and sustainability. This has created a demand for technologies such as industrial automation and control systems, simulator-training, equipment control and guidance, advanced mine-surveying technologies, underground mining and surface drilling technologies, and machine guidance and control systems, which are compatible with enterprise resource planning software solutions. A trend in mining technology has also been towards addressing the concerns of climate change and hence, reducing carbon footprints. The usage of more energy efficient equipment and reduction in fuel consumption are attempts in the right direction towards achieving reduced carbon footprints. The industry is increasingly seeking to develop solutions capable of electrifying mining equipment to eliminate diesel from its power source mix, therefore reducing greenhouse gas emissions. Internet of Things (IoT), an emerging network technology, can potentially transform the mining industry by creating new ways of maintaining mine safety and productivity. The convergence of IoT and advanced data analytics help in corroborating predictive maintenance, operational optimization, high equipment efficiency. People are looking for solutions which enables them to get Real time data for Decision-making and improving the efficiency of work.”
Chris Currie, Service Line Manager, FLSmidth, said, “As part of its dedication to providing top-tier screening media solutions tailored to meet the rigorous demands of commodity areas, FLS has brought to market its NexGen polyurethane screen media panel. Designed to offer long wear life, the NexGen polyurethane panel is ideally suited for early stage screens and trommels where high abrasion is the order of the day. Due to its extremely durable properties, it lasts longer than rubber or standard polyurethane in high impact applications. In some instances, it has been proven to offer double the screen panel wear life of rubber in these high-abrasion environments. With increased wear life also comes a significant reduction in waste not just in the material itself, but also in the supply chain. Less frequent panel changes mean that there is less energy used, less transport required and less stock needed, which in turn is a huge sustainability tick for our customers.”